Commercial Building HVAC Maintenance And Why Its Important
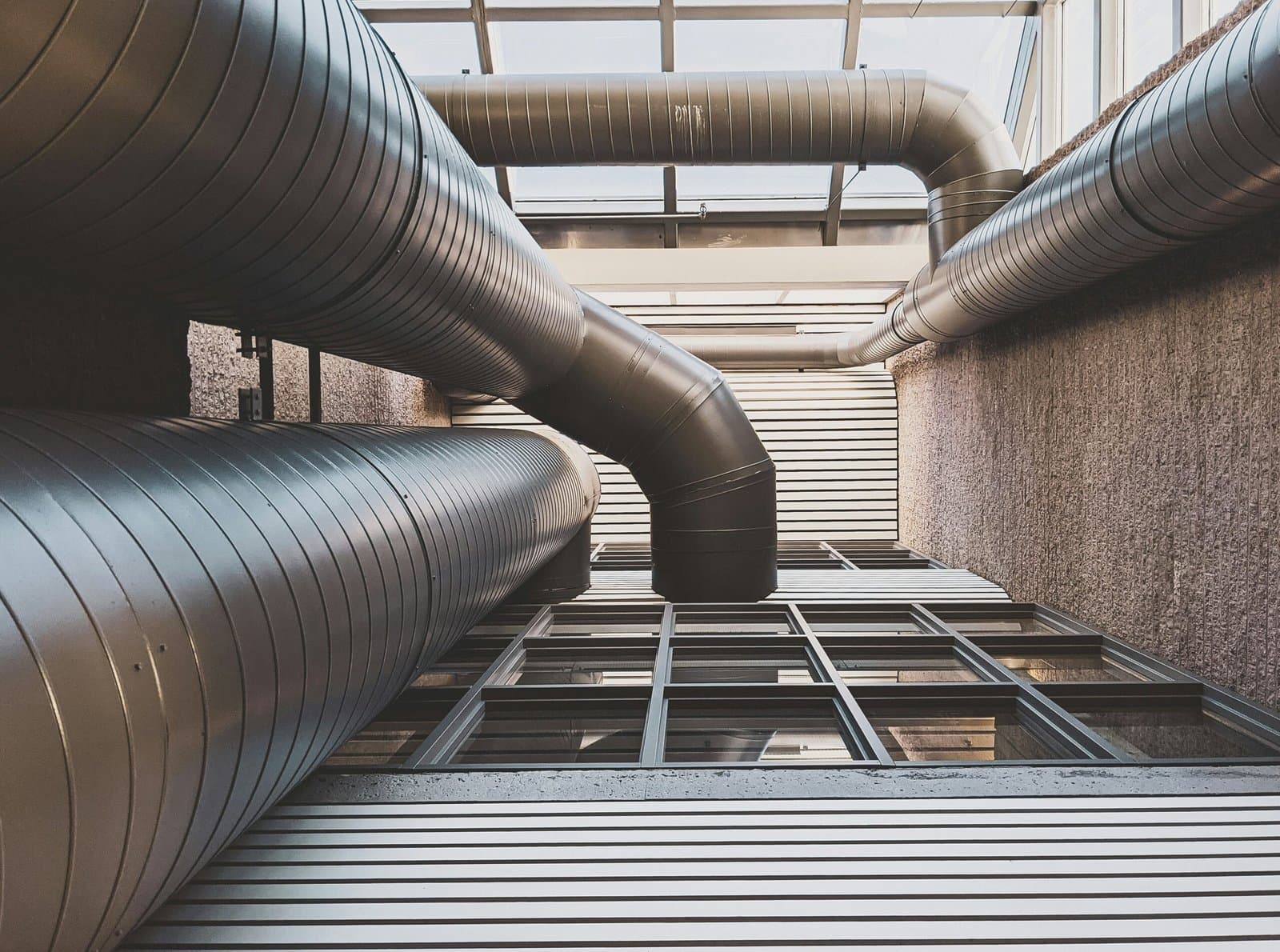
Proper HVAC maintenance is essential for commercial buildings, impacting everything from energy efficiency to occupant comfort and regulatory compliance. Facility managers and business owners must prioritize preventative maintenance to extend system lifespan, reduce energy costs, and improve air quality while ensuring compliance with industry regulations.
This guide covers key HVAC maintenance strategies for office buildings, warehouses, retail spaces, hospitals, and industrial facilities, along with common issues and troubleshooting tips.
Why HVAC Maintenance Matters for Commercial Buildings
A well-maintained HVAC system provides:
- Energy Efficiency – Dirty filters, clogged coils, and poor airflow force HVAC systems to work harder, increasing energy consumption.
- Cost Savings – Regular maintenance prevents expensive repairs and extends the lifespan of HVAC equipment.
- Improved Air Quality – Clean air filters and ducts reduce pollutants and allergens, improving occupant health.
- Regulatory Compliance – HVAC systems must meet industry standards, such as ASHRAE and OSHA guidelines.
Key Statistics on HVAC Maintenance and Efficiency
- HVAC systems account for 40% of total energy use in commercial buildings. (U.S. Department of Energy)
- Proper maintenance can reduce energy consumption by 15-20% annually. (EPA)
- 80% of HVAC failures are linked to lack of maintenance. (Facility Management Journal)
Preventative HVAC Maintenance Best Practices
1. Regular Filter Replacements
HVAC filters trap dust, debris, and allergens, preventing them from circulating through the building. However, dirty filters reduce efficiency and put stress on the system.
Best Practices:
- Replace filters every 1-3 months, depending on usage and air quality.
- Use high-efficiency particulate air (HEPA) filters for better air quality.
- Schedule filter inspections as part of routine maintenance.
2. Cleaning and Inspecting Coils
HVAC coils (evaporator and condenser) transfer heat efficiently, but dirt and debris accumulation can reduce system performance.
Best Practices:
- Clean coils at least twice a year to maintain efficiency.
- Ensure surrounding areas are free from dust and debris.
- Check for signs of corrosion or refrigerant leaks.
3. Checking Ductwork for Leaks
Leaky ducts cause HVAC systems to lose conditioned air, leading to higher energy costs and inconsistent indoor temperatures.
Best Practices:
- Inspect ducts for leaks, blockages, and insulation damage.
- Seal leaks using aerosol-based sealants or duct tape.
- Conduct professional air balance testing to ensure proper airflow.
4. Thermostat Calibration and Optimization
A well-calibrated thermostat ensures accurate temperature control, reducing energy waste and improving comfort.
Best Practices:
- Check thermostat settings seasonally and recalibrate if necessary.
- Upgrade to programmable or smart thermostats for automated energy savings.
- Set optimal temperature ranges: 68-72°F in winter and 74-78°F in summer.
5. Refrigerant Level Checks and Leak Detection
Low refrigerant levels reduce cooling efficiency and can damage the compressor, leading to costly repairs.
Best Practices:
- Inspect refrigerant levels annually.
- Identify and repair leaks promptly.
- Use EPA-compliant refrigerants to meet environmental regulations.
6. Routine Inspection of Electrical Components
Faulty electrical connections can cause system failures and increase fire hazards.
Best Practices:
- Check for loose or corroded connections.
- Test capacitors and contactors for wear.
- Ensure proper voltage levels to avoid overheating.
Common HVAC Issues and Troubleshooting Tips
-
Uneven Heating or Cooling
- Check for blocked vents and duct leaks.
- Ensure fans and dampers are functioning properly.
-
Strange Noises (Banging, Whistling, or Grinding)
- Inspect belts, motors, and bearings for wear.
- Tighten loose components to prevent vibrations.
-
Poor Airflow
- Replace dirty air filters.
- Inspect ducts for obstructions or leaks.
-
High Energy Bills
- Upgrade to energy-efficient HVAC systems.
- Schedule professional maintenance to optimize performance.
Ensuring Compliance with Industry Regulations
Facility managers and business owners must comply with ASHRAE (American Society of Heating, Refrigerating and Air-Conditioning Engineers) and OSHA (Occupational Safety and Health Administration) standards to maintain safe and efficient HVAC systems.
Key Compliance Areas:
- Indoor Air Quality (IAQ) Standards – Maintain proper ventilation and filtration.
- Energy Efficiency Standards – Meet local energy codes and optimize HVAC performance.
- Refrigerant Regulations – Use eco-friendly refrigerants and properly dispose of old ones.
LEED Certification and HVAC Sustainability
For businesses pursuing LEED (Leadership in Energy and Environmental Design) certification, HVAC efficiency plays a crucial role. Energy-efficient systems contribute to lower carbon footprints, improved building performance, and higher property values.
The Cost-Saving Benefits of Proactive HVAC Maintenance
Short-Term Savings
- Reduced repair costs by 30-40% with preventative maintenance.
- Lower monthly energy bills due to optimized system performance.
Long-Term Savings
- Extended equipment lifespan by 5-10 years.
- Increased property value through sustainable building upgrades.
Partner with APS Industrial Services for Reliable HVAC Maintenance
Proper HVAC maintenance requires expertise, routine inspections, and energy-efficient upgrades to maximize system performance. APS Industrial Services provides comprehensive commercial HVAC maintenance solutions to keep your building’s systems running efficiently and cost-effectively.
Contact APS Industrial Services today to schedule your HVAC maintenance and optimize your commercial building’s performance.
Newsletter
Don't miss a thing!
Sign up to receive daily news
Recent Posts
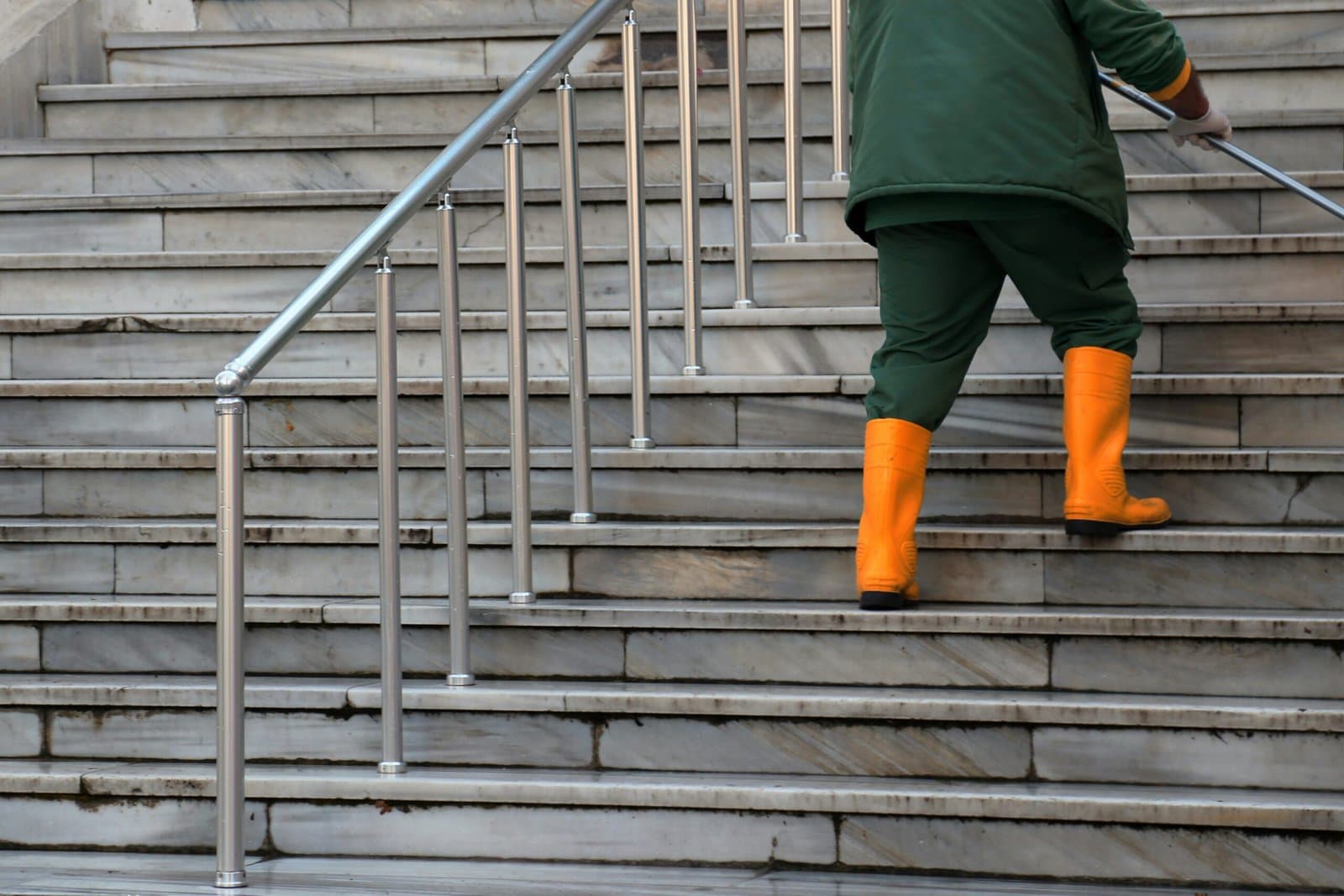
february 21, 2025
Green Cleaning Practices for Commercial Buildings
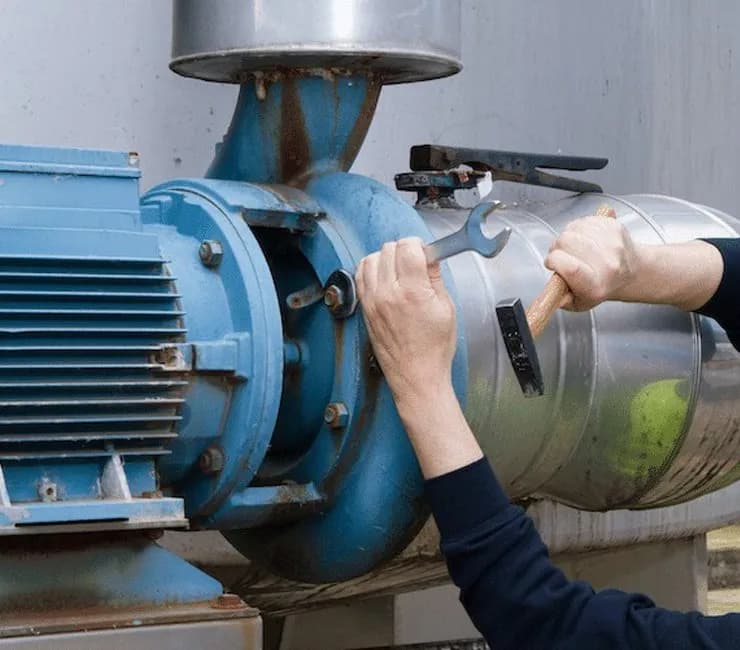
february 21, 2025
Maintaining Industrial Facilities: A Comprehensive Guide
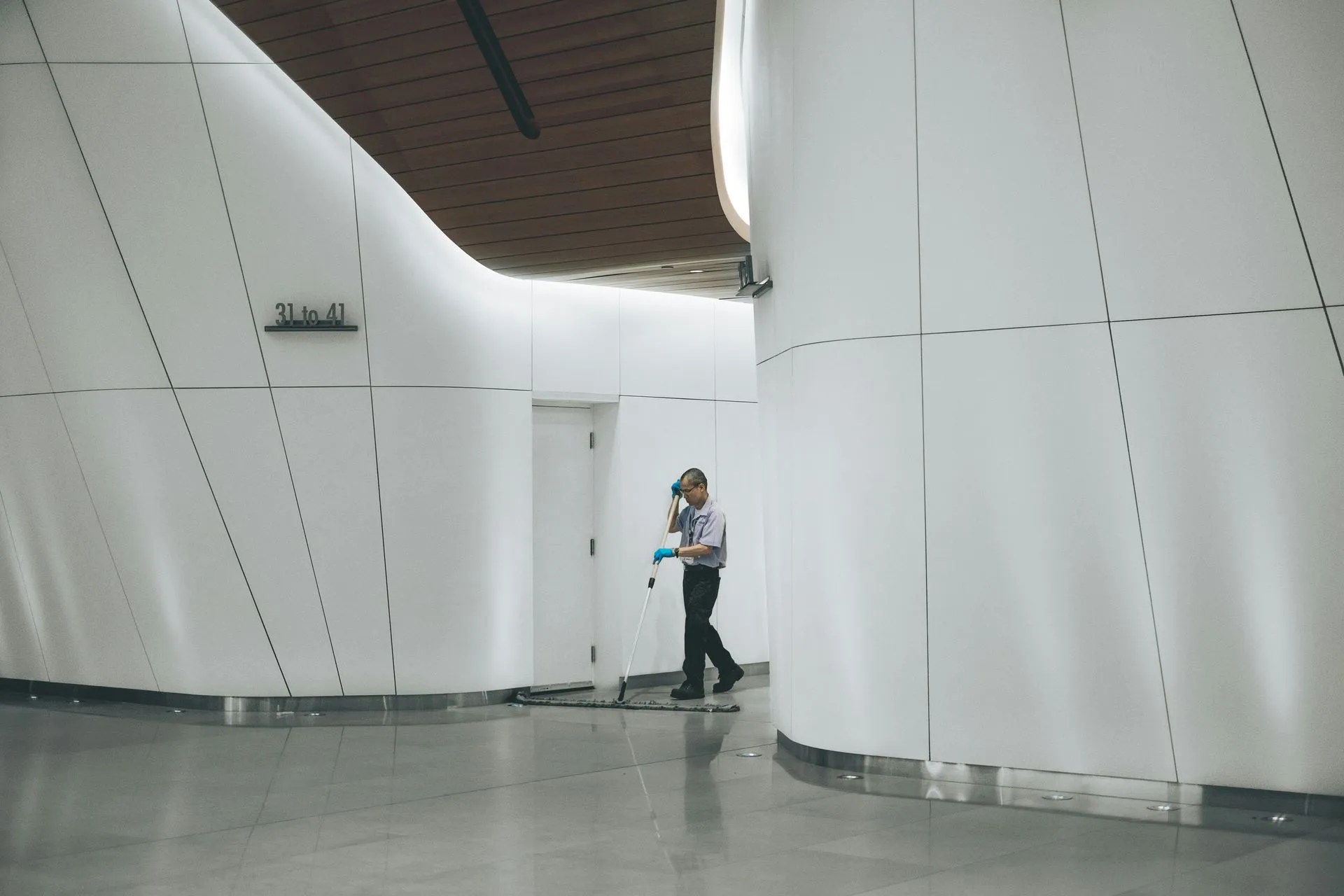
december 18, 2024
Facility Deep Cleaning and Restoration Services for Industrial Facilities
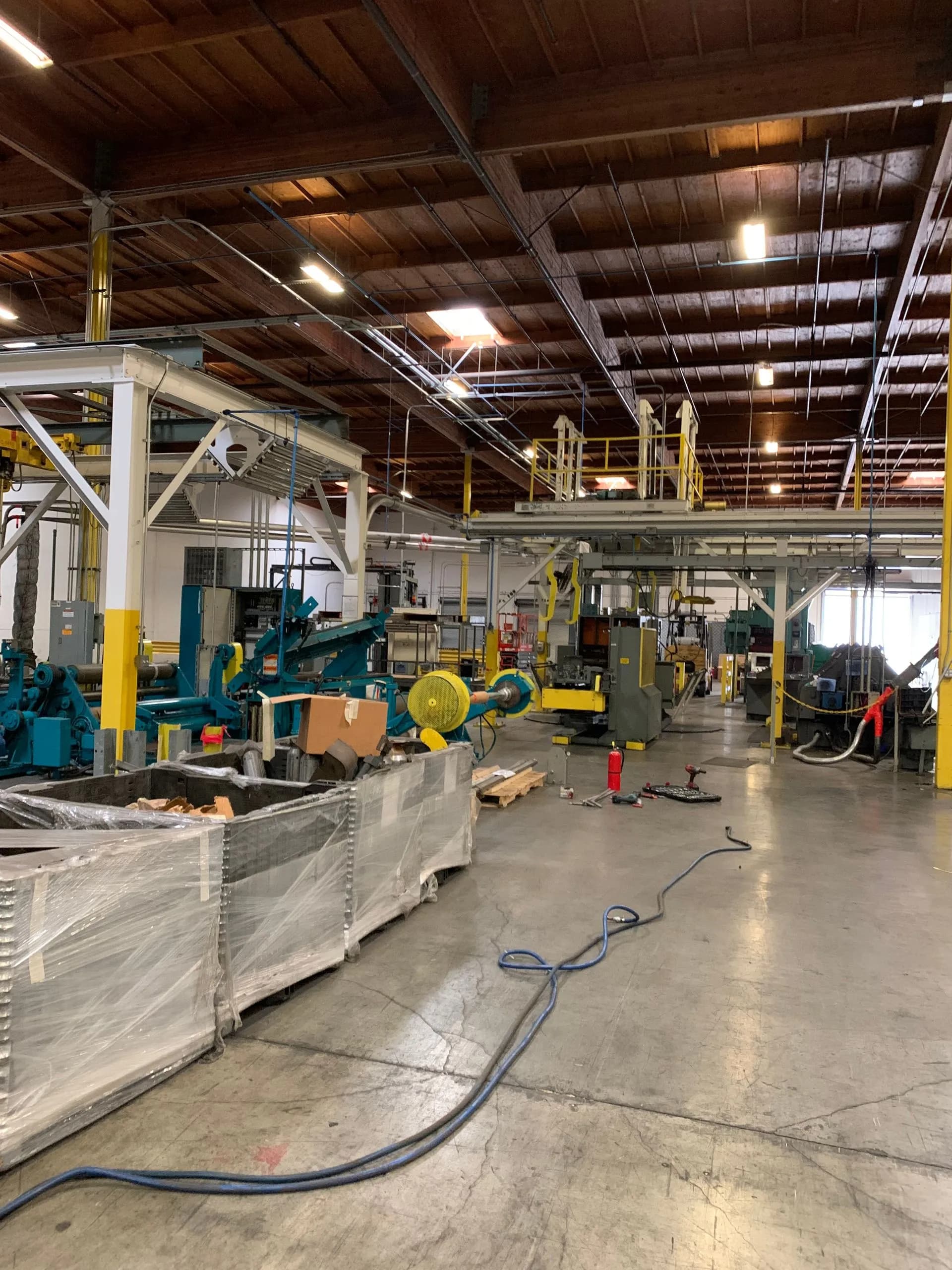
december 6, 2024
Facility Installation: From Site Preparation to Final Testing
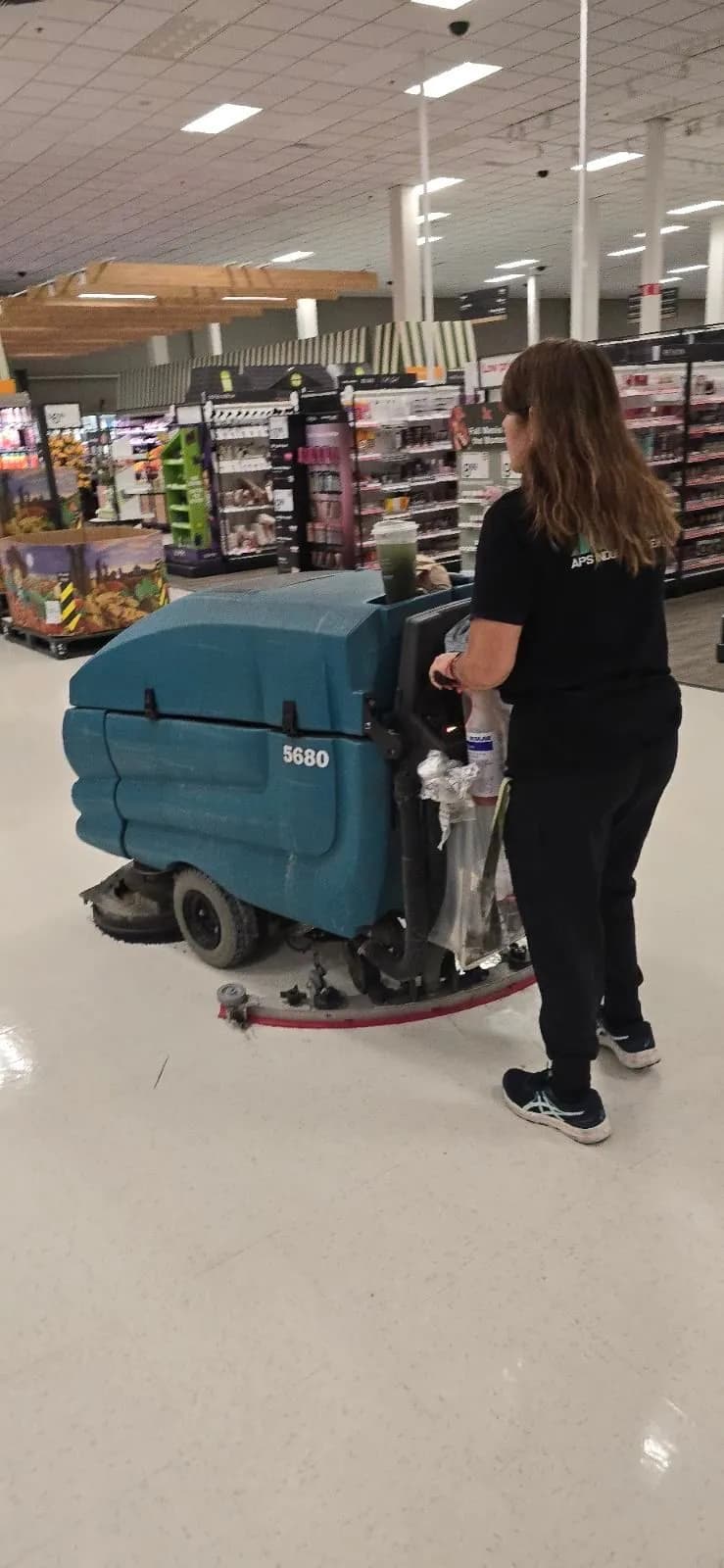
november 30, 2024