Maintaining Industrial Facilities: A Comprehensive Guide
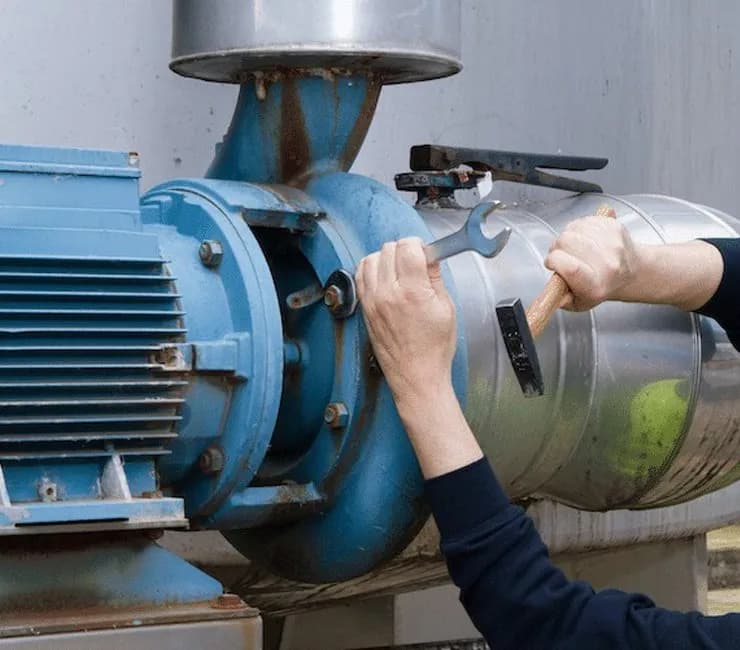
Industrial facilities are the backbone of countless businesses, housing critical equipment, employees, and operations that drive productivity and revenue. However, maintaining industrial facilities is no small feat. Facility managers and business owners must juggle preventive maintenance, safety regulations, equipment longevity, and cost efficiency—all while ensuring minimal downtime. In this guide, we’ll explore best practices for maintaining industrial facilities, addressing common challenges, and highlighting strategies to optimize operations.
The Importance of Industrial Facility Maintenance
A well-maintained industrial facility ensures safety, efficiency, and compliance with regulatory standards. Poor maintenance can lead to unplanned downtime, costly repairs, safety hazards, and regulatory fines. A structured maintenance strategy helps prevent these risks, ensuring smooth operations and long-term cost savings.
Key Areas of Industrial Facility Maintenance
1. Equipment Maintenance & Upkeep
Industrial equipment is the heart of a facility’s operations, and its maintenance should be a top priority. A mix of preventive and predictive maintenance can significantly reduce failures and extend equipment lifespan.
- Preventive Maintenance: Scheduled inspections, lubrication, and part replacements to prevent breakdowns.
- Predictive Maintenance: Using sensors and data analytics to predict failures before they occur.
- Reactive Maintenance: Emergency repairs when equipment fails unexpectedly.
Best Practices:
✔ Implement a Computerized Maintenance Management System (CMMS) to track maintenance schedules.
✔ Train employees on proper equipment handling and troubleshooting techniques.
✔ Conduct regular performance audits to identify inefficiencies.
2. Structural Integrity & Building Maintenance
The physical structure of an industrial facility must be well-maintained to ensure safety and operational efficiency. Over time, buildings face wear and tear from heavy machinery, environmental factors, and foot traffic.
Key Maintenance Areas:
- Roofing & Insulation: Preventing leaks, heat loss, and structural damage.
- Floors & Foundations: Addressing cracks, uneven surfaces, and load-bearing capacity.
- Doors & Docking Areas: Ensuring seamless operation for logistics and material handling.
Best Practices:
✔ Conduct regular structural assessments and repairs.
✔ Use industrial-grade materials for renovations and updates.
✔ Ensure proper drainage systems to prevent water damage.
3. Safety & Compliance
Industrial facilities must adhere to OSHA regulations and other industry-specific safety standards. Ignoring safety compliance can lead to fines, legal liability, and workplace injuries.
Key Focus Areas:
- Fire Safety: Routine inspections of fire suppression systems, extinguishers, and emergency exits.
- Ventilation & Air Quality: Maintaining HVAC systems to prevent exposure to hazardous substances.
- Workplace Ergonomics: Ensuring safe working conditions for employees handling heavy machinery.
Best Practices:
✔ Conduct regular safety drills and compliance training.
✔ Implement a hazard identification and reporting system.
✔ Schedule third-party safety audits to stay up-to-date with regulations.
4. Energy Efficiency & Sustainability
Reducing energy consumption not only lowers operational costs but also supports sustainability initiatives. Many facilities now integrate energy-efficient solutions to minimize their carbon footprint.
Energy-Saving Strategies:
- LED Lighting & Motion Sensors: Reduce electricity waste.
- HVAC Optimization: Regular maintenance and smart automation for better efficiency.
- Solar & Renewable Energy Solutions: Supplementing power needs with sustainable sources.
Best Practices:
✔ Conduct energy audits to identify wasteful areas.
✔ Upgrade to energy-efficient equipment where possible.
✔ Establish green initiatives such as recycling programs and waste reduction.
Proactive vs. Reactive Maintenance: Which is Better?
While reactive maintenance is sometimes necessary, a proactive approach is more cost-effective and reliable.
- Proactive Maintenance: Prevents costly failures, extends asset lifespan, and improves efficiency.
- Reactive Maintenance: Leads to unexpected costs, production halts, and increased safety risks.
Implementing a mix of preventive and predictive maintenance is the most effective way to balance costs and efficiency.
Partnering with Reliable Maintenance Providers
Facility managers and business owners don’t have to handle maintenance alone. Partnering with a professional service provider can ensure expert maintenance, compliance, and long-term cost savings.
At APS Industrial Services, we specialize in maintaining industrial facilities and providing tailored solutions to keep your operations running smoothly. From equipment upkeep to structural repairs and compliance management, our expert team is ready to assist.
Contact APS Industrial Services today for reliable building maintenance solutions!
Newsletter
Don't miss a thing!
Sign up to receive daily news
Recent Posts
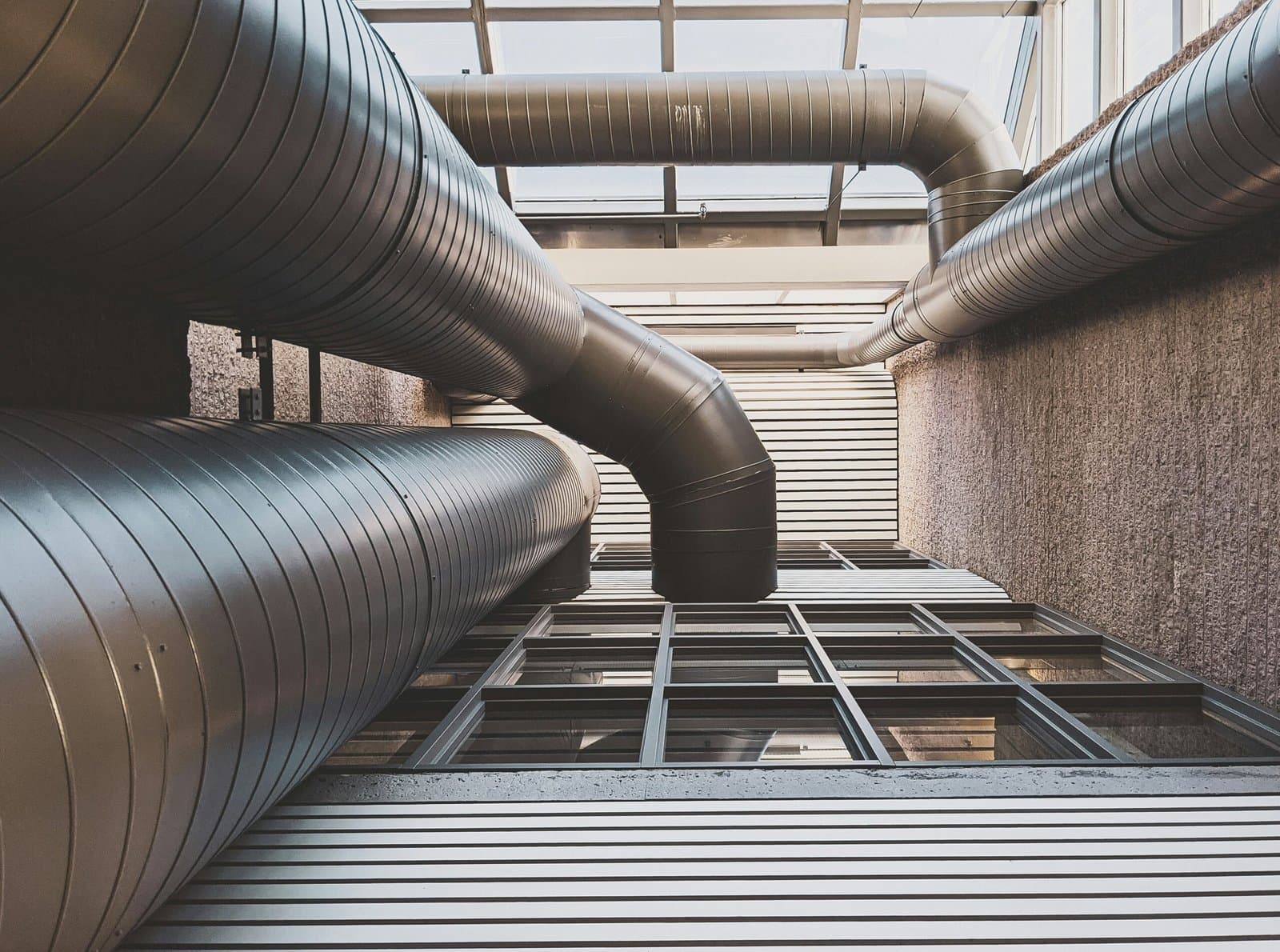
february 22, 2025
Commercial Building HVAC Maintenance And Why Its Important
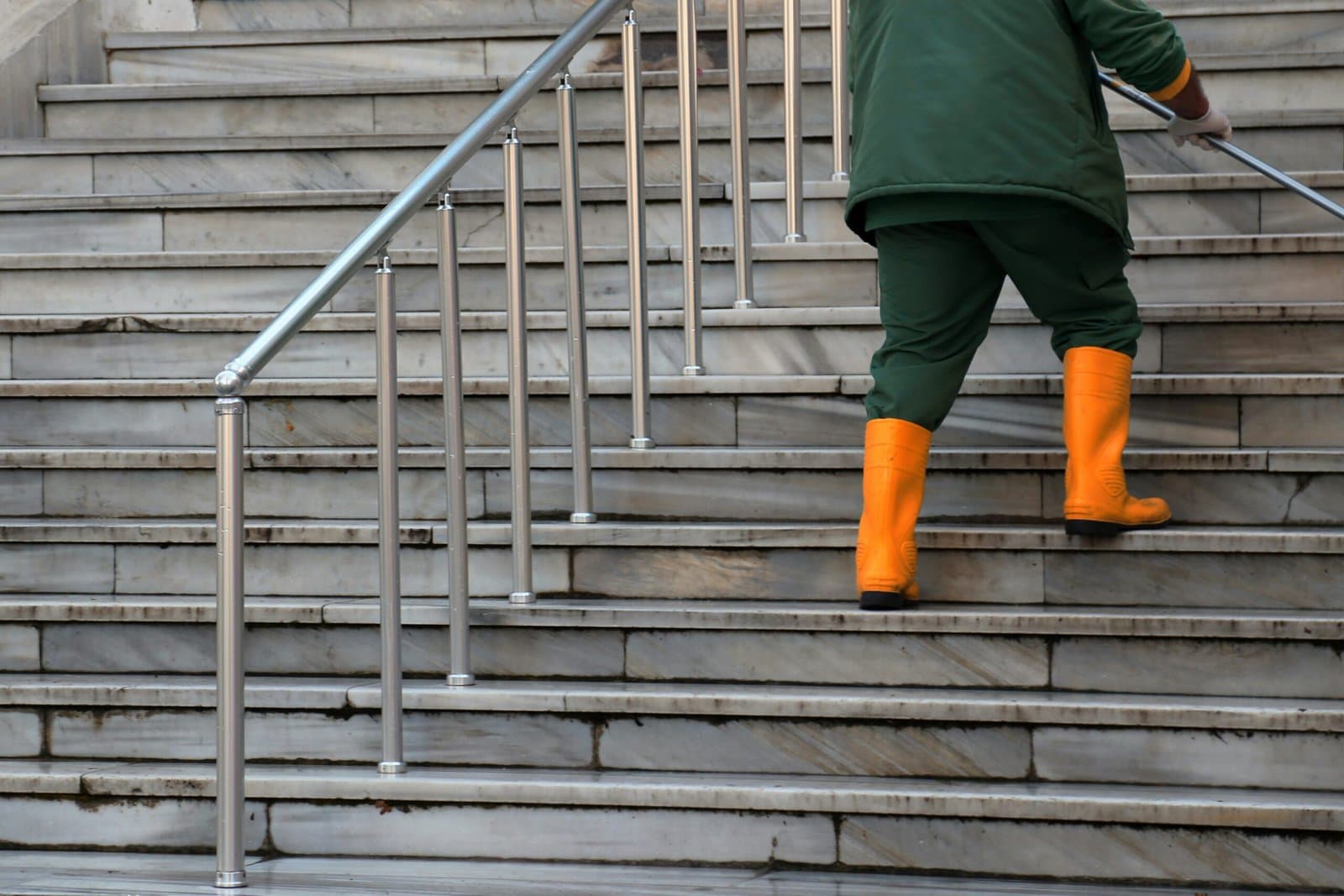
february 21, 2025
Green Cleaning Practices for Commercial Buildings
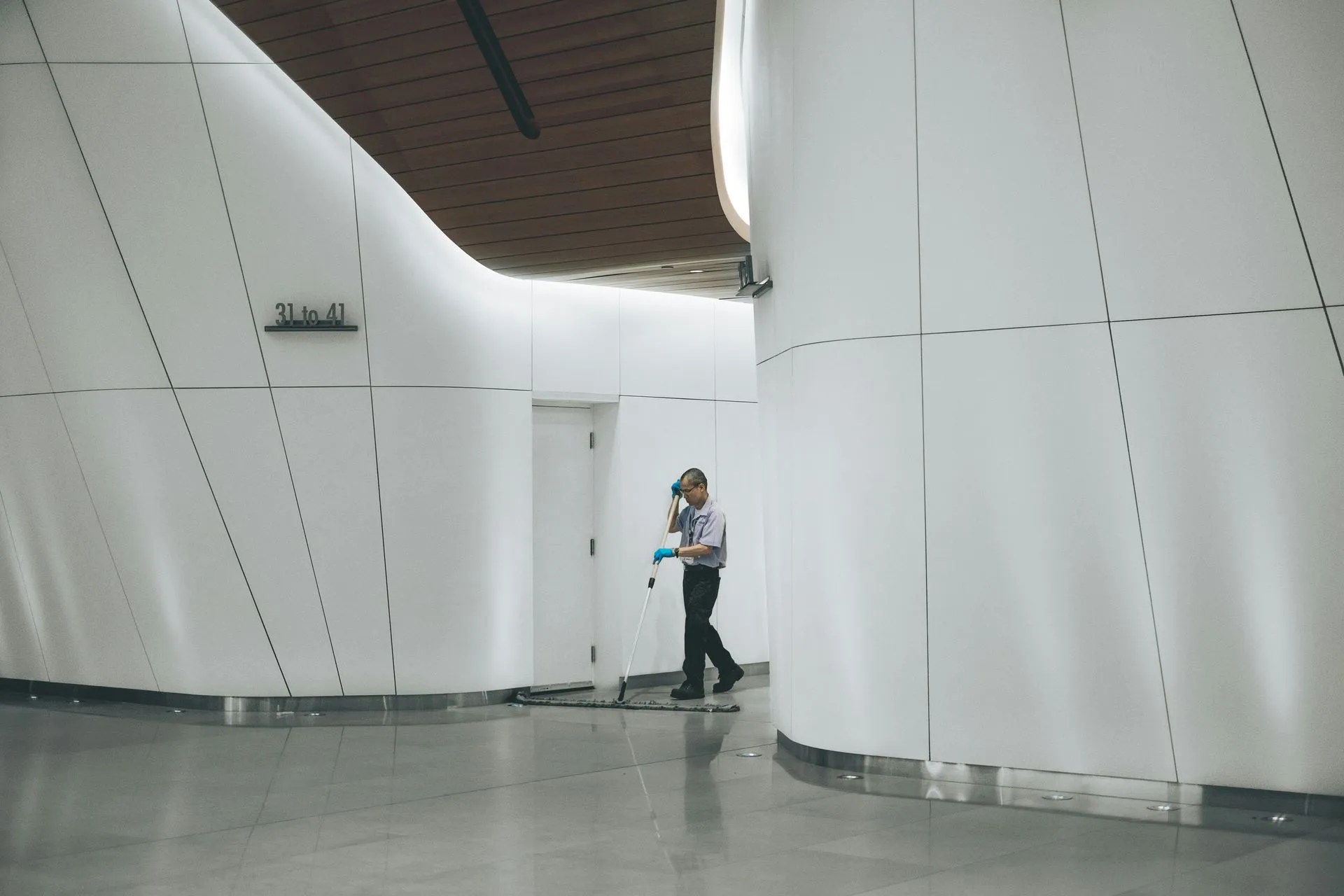
december 18, 2024
Facility Deep Cleaning and Restoration Services for Industrial Facilities
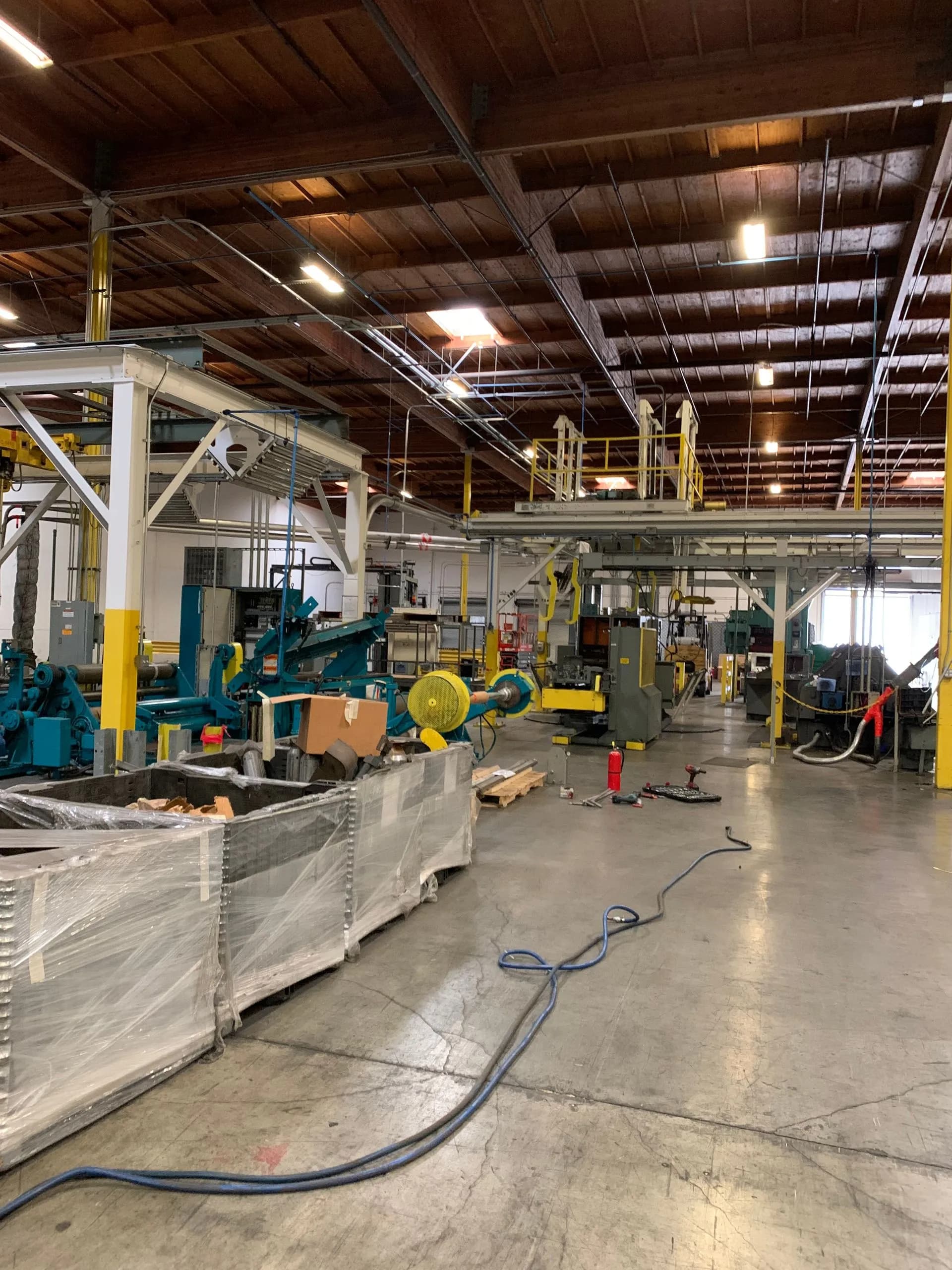
december 6, 2024
Facility Installation: From Site Preparation to Final Testing
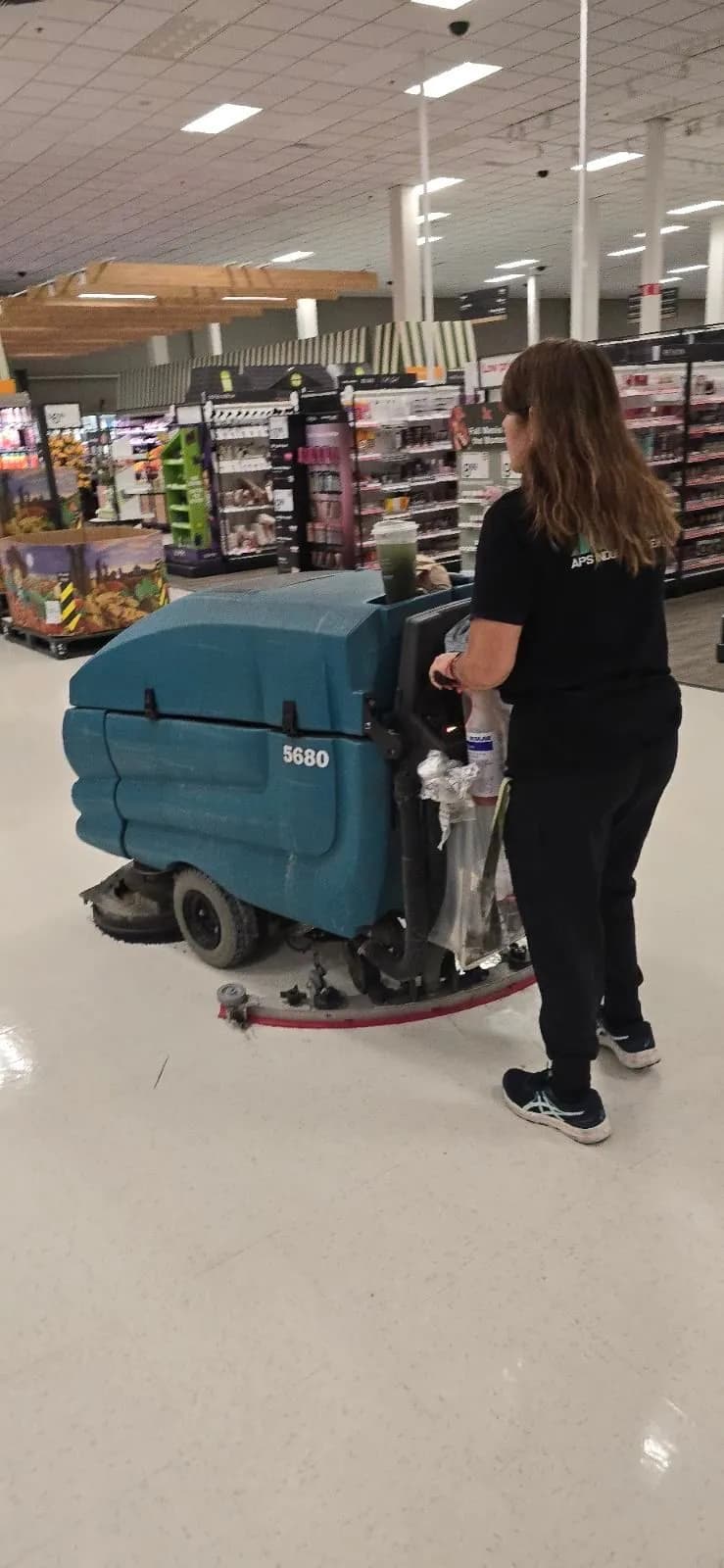
november 30, 2024