Machinery Moving: Proper Rigging for Safe Lifting & Transport
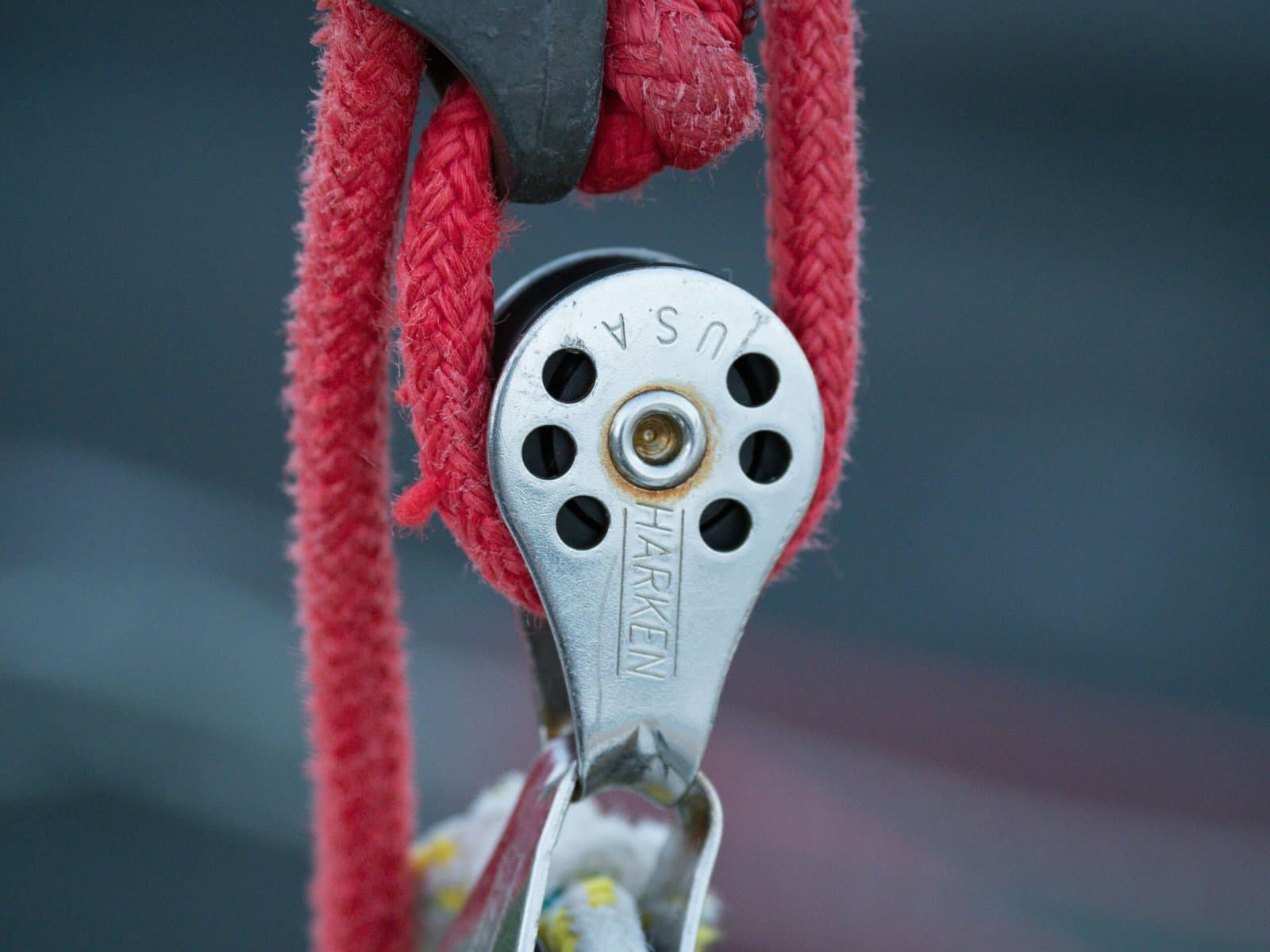
When it comes to machinery moving, proper rigging techniques are essential to ensure safety, efficiency, and compliance with industry standards. Rigging involves preparing, securing, and lifting heavy equipment for transportation and installation, requiring precise planning and execution. Mistakes in rigging can lead to severe injuries, equipment damage, and costly downtime.
This guide covers key rigging best practices that business owners and facility managers should know when moving machinery. From equipment selection to load calculations and OSHA compliance, we’ll break down the essential steps to ensure safe and successful rigging operations.
1. Understanding Load Characteristics
Before lifting any machinery, a detailed assessment of the load is necessary. Key factors to evaluate include:
-
Weight and Center of Gravity – Identifying the load’s weight and balance point prevents tipping and ensures stable lifting.
-
Shape and Size – Irregularly shaped machinery may require custom rigging solutions to maintain stability.
-
Attachment Points – Using the right lifting points prevents strain on weak areas of the equipment.
-
Structural Integrity – Ensuring the load can handle the stresses of being lifted and transported.
Industry Example
According to the Bureau of Labor Statistics (BLS), improper load balancing is one of the top causes of industrial rigging accidents. A miscalculated center of gravity can lead to load shifts, increasing the risk of tip-overs.
2. Selecting the Right Rigging Equipment
The success of a rigging operation depends on using the appropriate lifting equipment. Common rigging tools include:
-
Slings (Wire Rope, Chain, Synthetic) – Used to secure loads to lifting equipment. Each type has a different weight capacity and flexibility.
-
Shackles – Connect rigging components and should be chosen based on the load’s weight and angle.
-
Hoists and Cranes – Essential for lifting, with load capacity carefully matched to the machine being moved.
-
Spreader Bars and Lifting Beams – Help distribute weight evenly, reducing stress on rigging components.
-
Turnbuckles and Hooks – Adjust tension and secure connections in the rigging setup.
Pro Tip:
Always inspect rigging equipment before use. OSHA requires frequent inspections of lifting devices to prevent failures due to wear and tear.
3. Rigging Safety Standards and OSHA Compliance
Ensuring compliance with OSHA (Occupational Safety and Health Administration) standards is critical for workplace safety. The following regulations apply to machinery moving and rigging operations:
-
OSHA 1926.251 – Covers rigging equipment for material handling.
-
ASME B30.9 – Regulates the use of slings in rigging operations.
-
OSHA 1910.184 – Outlines safe lifting practices for industrial rigging.
Violations of these standards can result in fines and increased liability risks. Ensuring that riggers are trained and certified is a crucial step in preventing workplace incidents.
4. Proper Load Securing and Lifting Techniques
Load Securing Best Practices
-
Use multiple attachment points to distribute force evenly.
-
Verify that all rigging components are rated for the intended weight.
-
Double-check connections and use safety latches where applicable.
Lifting Best Practices
-
Always lift loads vertically to avoid unintended swinging.
-
Maintain a slow and steady lifting motion to reduce dynamic forces.
-
Keep workers clear of the fall zone in case of rigging failure.
Case Study: Avoiding a Costly Machinery Drop
In 2021, a manufacturing plant suffered $500,000 in damages when an improperly rigged CNC machine shifted mid-lift. Investigators found that the riggers failed to properly assess the center of gravity, leading to the machine tipping off the slings. A thorough pre-lift calculation and secondary securing method could have prevented the incident.
5. Transporting Machinery Safely
Once machinery is lifted, the next step is safe transport to its final location. Follow these best practices:
-
Use Heavy-Duty Tie-Downs – Chains and straps rated for the load’s weight prevent movement during transport.
-
Monitor Load Shifts – Regularly check securing points during transport, especially over long distances.
-
Adjust for Road Conditions – Consider low-clearance bridges, tight turns, and uneven roads when planning the route.
-
Work with Certified Machinery Movers – Professional services ensure compliance and prevent costly accidents.
6. Choosing the Right Machinery Moving Partner
While in-house teams can handle smaller rigging jobs, large-scale machinery moves require experienced professionals. APS Industrial Services specializes in safe and efficient rigging solutions, ensuring compliance with industry regulations and minimizing downtime.
By working with APS Industrial Services, businesses benefit from:
✅ Experienced rigging professionals
✅ Compliance with OSHA safety standards
✅ Minimized risk of equipment damage
✅ Efficient and cost-effective machinery relocation
Contact APS Industrial Services today to discuss your rigging and machinery moving needs.
Proper rigging techniques are critical for the safe lifting and transport of machinery. Business owners and facility managers must ensure compliance with industry best practices, including selecting the right rigging equipment, securing loads properly, and following OSHA safety standards. By partnering with professionals like APS Industrial Services, companies can minimize risks and ensure a smooth and safe machinery moving process.
Newsletter
Don't miss a thing!
Sign up to receive daily news
Recent Posts
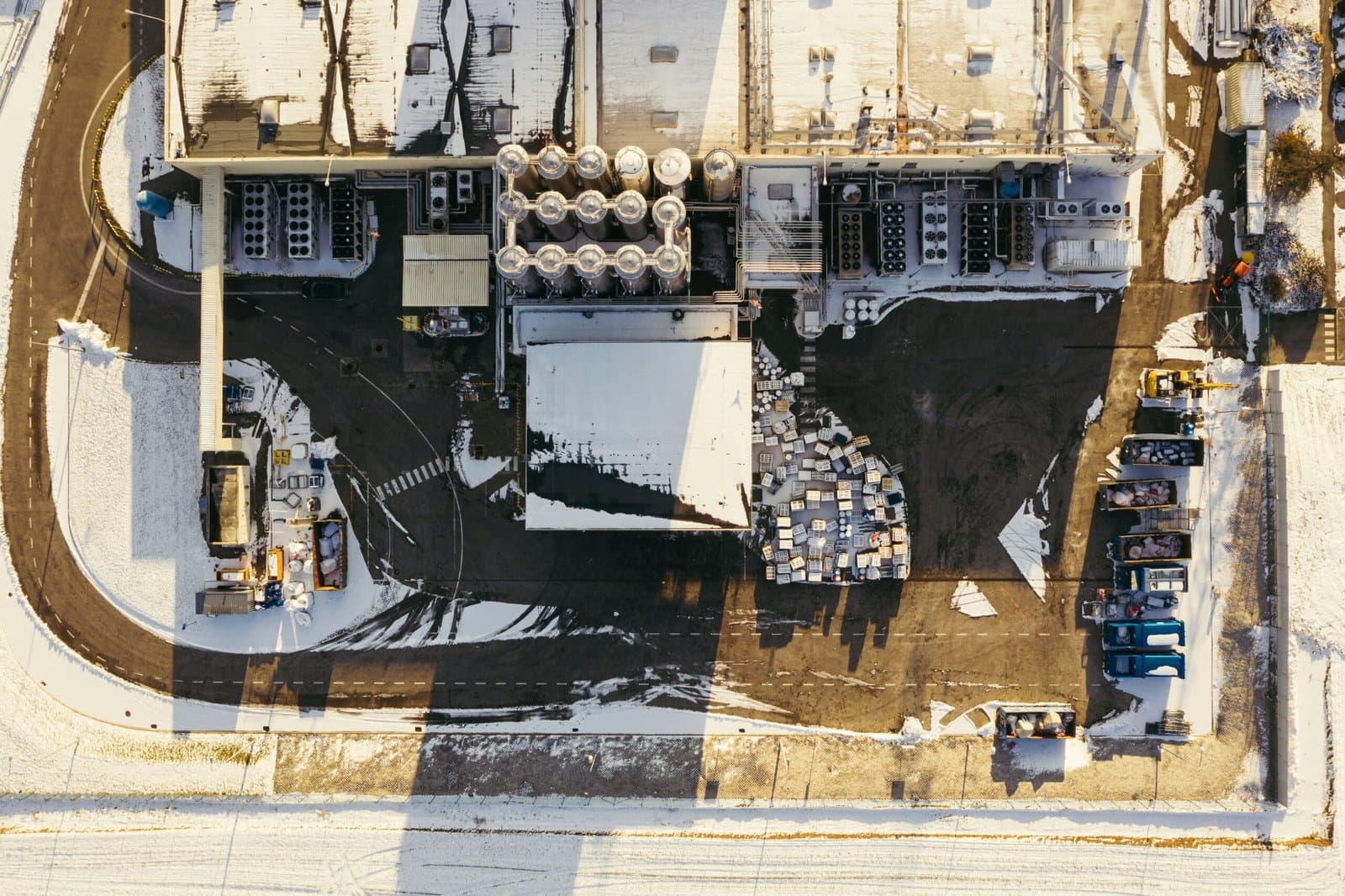
march 28, 2025
Industrial Facility Dismantling: Challenges & Solutions
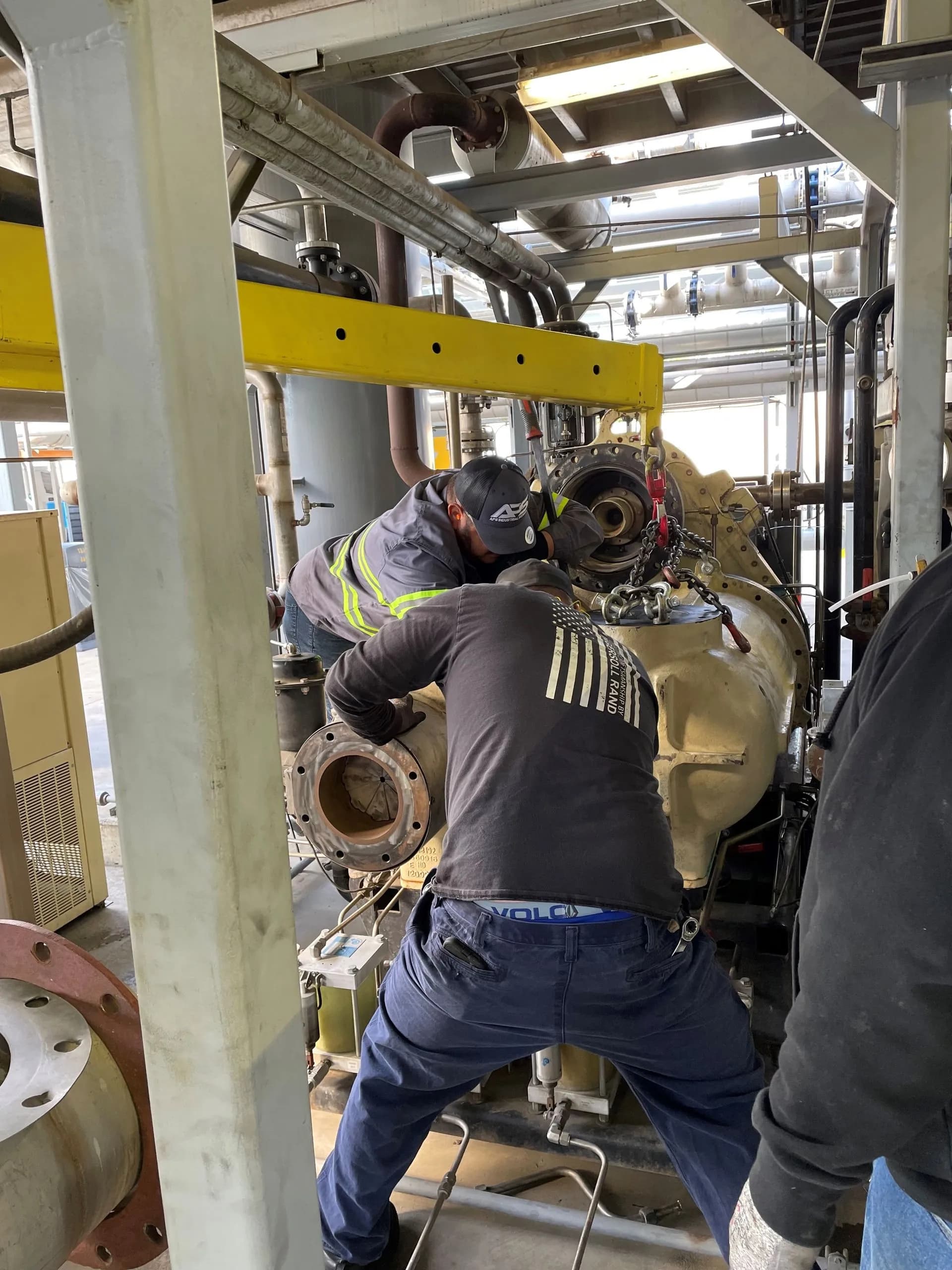
march 26, 2025
Machinery Moving: Protecting Your Facility
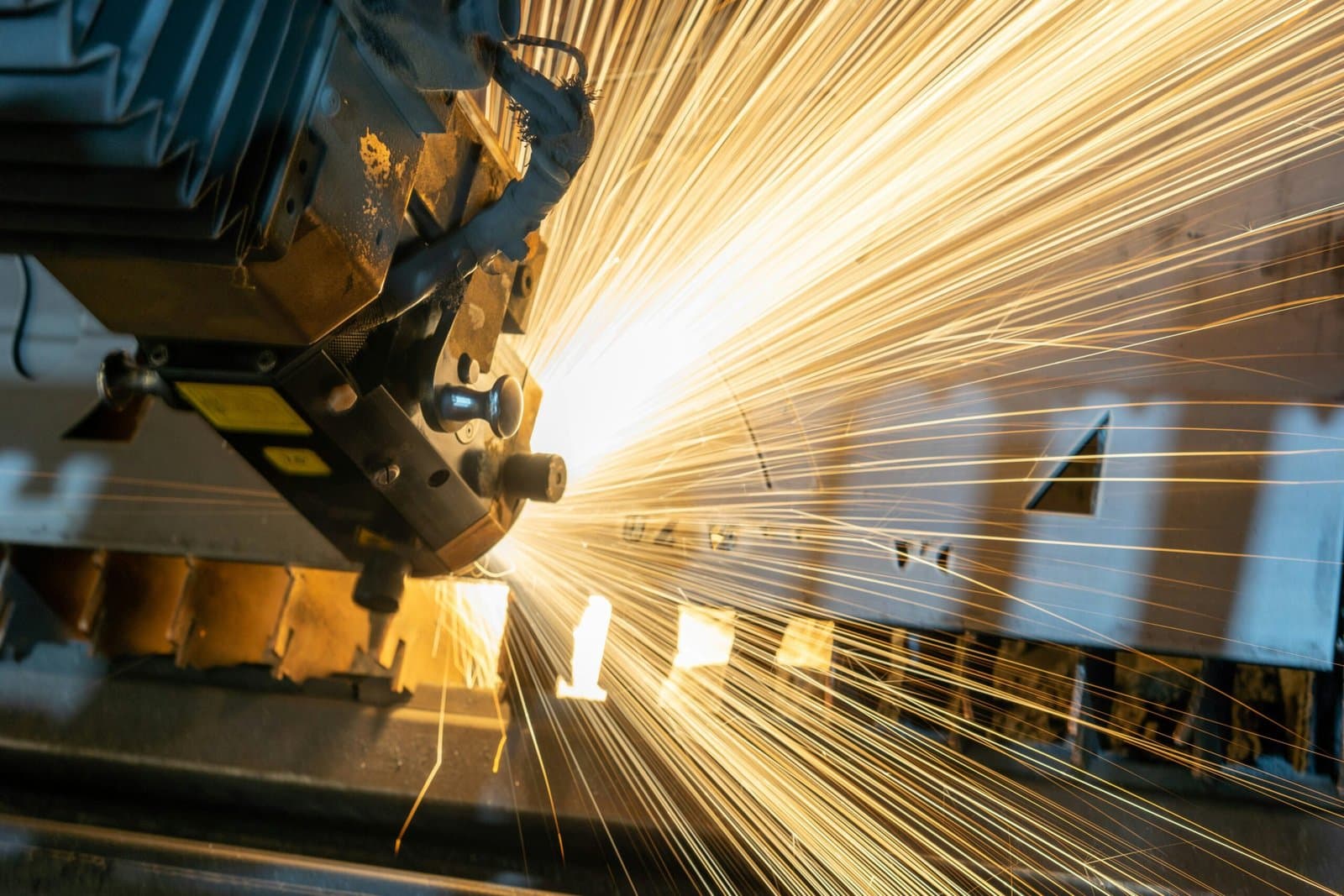
march 24, 2025
Manufacturing Rigging: Moving and Installing Heavy Machinery
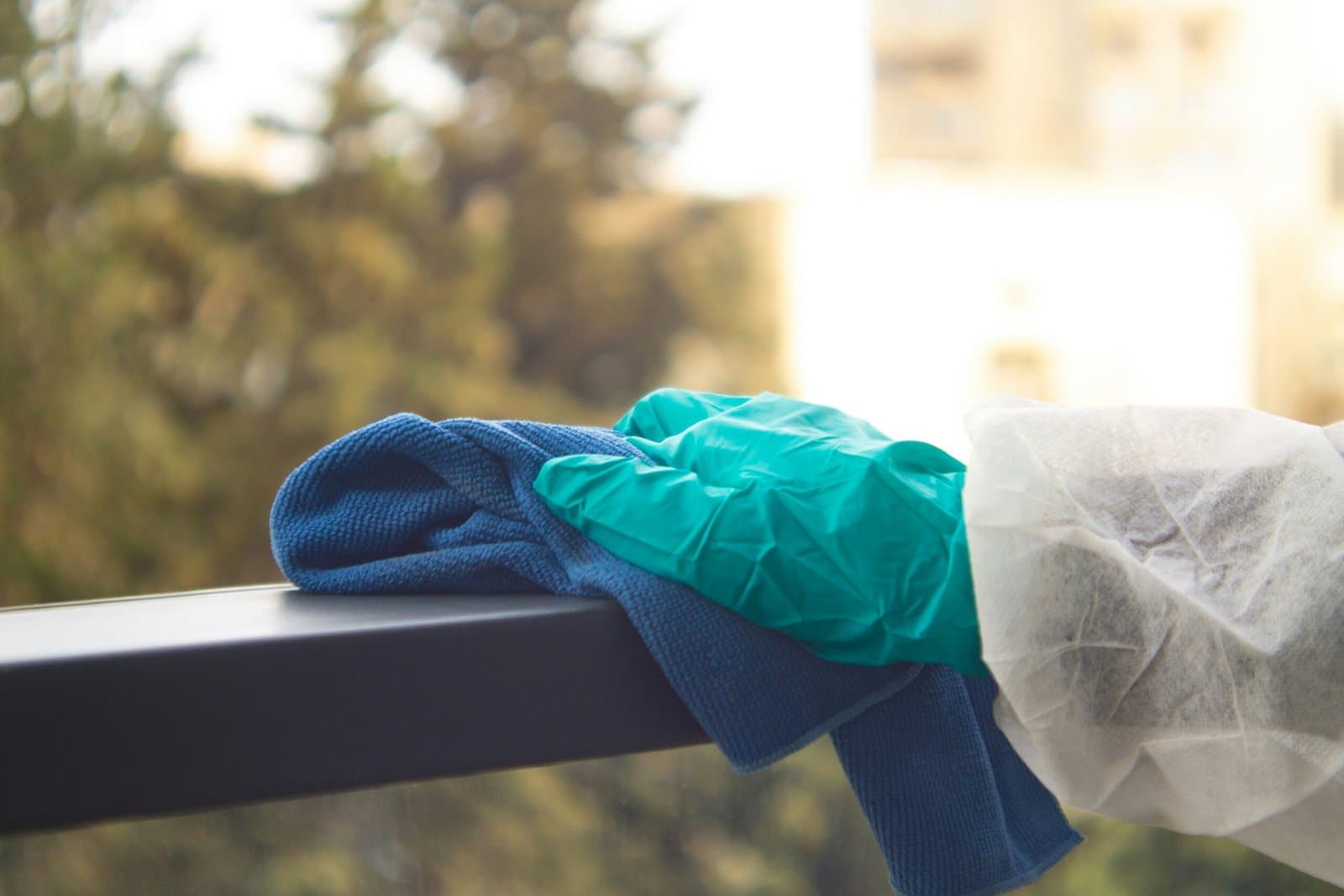
march 22, 2025
Commercial Office Cleaning: Enhancing Productivity & Employee Well-Being
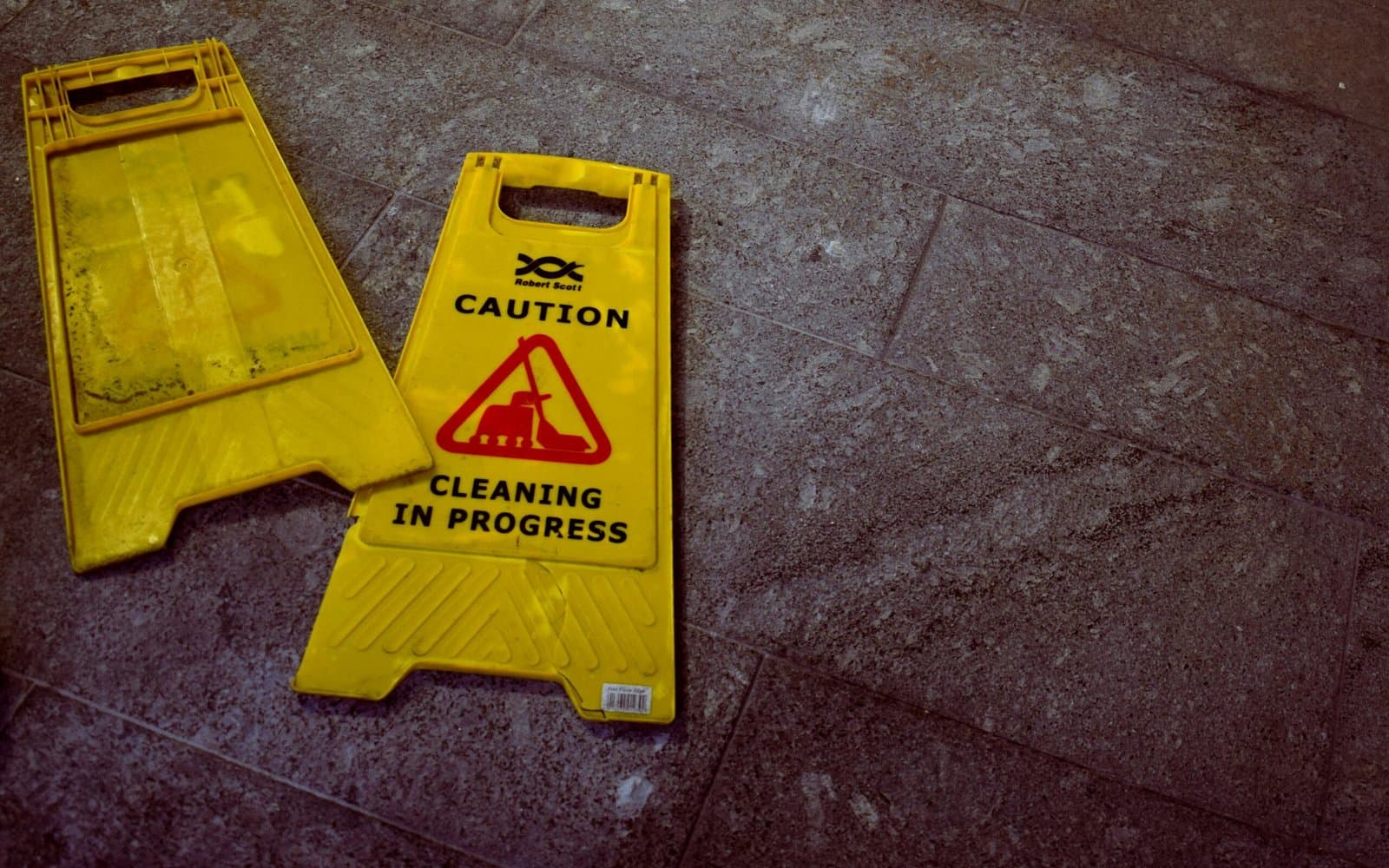
march 21, 2025