Machinery Moving: Protecting Your Facility
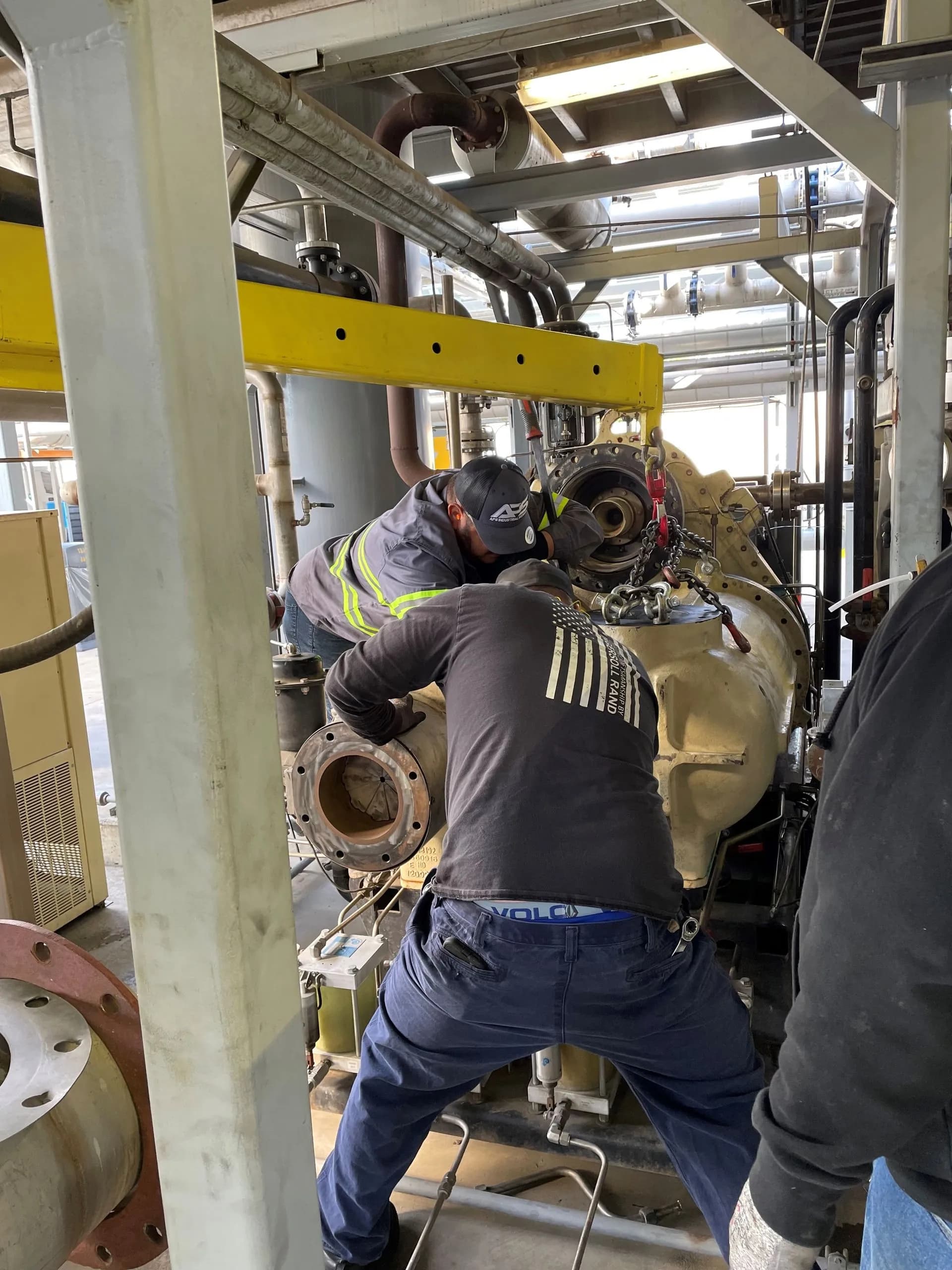
Moving heavy machinery within a facility is a complex and potentially risky task. Whether you’re relocating equipment for maintenance, upgrading to new machinery, or reorganizing production lines, it’s essential to focus on protecting both your assets and your facility throughout the process. Without careful planning, machinery moving can lead to unexpected damages to your building, machinery, or even equipment loss.
This blog will explore strategies for minimizing damage and disruption during the machinery moving process, ensuring a smooth operation that maintains the integrity of your facility and keeps downtime to a minimum.
The Importance of Careful Machinery Moving
Machinery moves are often necessary for improving production efficiency, upgrading equipment, or responding to facility expansion. However, improper handling during the move can result in:
-
Structural damage to floors, walls, or ceilings.
-
Scratches or dents to machinery.
-
Disruption to operations, leading to unnecessary downtime.
-
Workplace safety hazards, including worker injuries.
By adopting best practices and focusing on safety, facilities can reduce risks and ensure a seamless transition while avoiding costly damages or delays.
Planning for a Safe and Efficient Move
1. Conduct a Thorough Facility Assessment
The first step in protecting your facility during a machinery move is a comprehensive facility assessment. Before moving any machinery, evaluate the following:
-
Floor Load Capacity: Ensure the floor can support the weight of the machinery, especially when it’s in motion. Floor damage can occur if heavy equipment exceeds weight limits, causing cracks or uneven surfaces.
-
Obstacles and Clearance: Assess the path of the machinery to ensure there are no obstacles—such as pipes, doors, or low-hanging lights—that could obstruct or damage the move.
-
Access Points: Ensure all entryways, doors, and hallways are wide enough to accommodate the machinery, preventing accidental wall or doorframe damage.
Proper assessment helps identify potential risks and challenges, ensuring the move proceeds smoothly and without unexpected interruptions.
2. Use Proper Rigging and Lifting Equipment
To avoid damaging your facility’s infrastructure, the right rigging equipment is crucial. Heavy machinery should always be moved using industry-standard equipment such as:
-
Cranes, forklifts, and hoists for lifting.
-
Rollers or machine skates for easy movement across floors without scraping or denting surfaces.
-
Slings and spreader bars for secure lifting and weight distribution, reducing the risk of tipping or uneven load shifting.
Using specialized equipment ensures that heavy machines are safely lifted and moved without damaging the facility’s floors, walls, or ceilings.
3. Protect Your Facility’s Surfaces
Protecting the surfaces within your facility is crucial. Here are several methods to minimize damage during machinery moving:
-
Floor Protection: Use heavy-duty floor protection materials like plywood sheets or foam pads to shield floors from scratches, cracks, or dents during the move.
-
Wall Padding: Install temporary padding or soft barriers along walls or any other potential contact points to prevent scratches or dents from machinery contact.
-
Doorway Protection: If machinery must pass through doorways or tight spaces, consider using corner guards or inflatable bumpers to protect walls and door frames from damage.
By covering sensitive areas, you reduce the chances of physical damage to your building, machinery, or other assets.
4. Ensure Proper Training and Qualified Personnel
One of the most important aspects of protecting your facility is ensuring that only trained professionals handle the move. Rigging teams should be experienced and well-versed in proper machinery handling and safety protocols. They should:
-
Be certified in equipment operation, rigging, and safety.
-
Understand how to maneuver machinery through tight spaces without causing damage to floors or infrastructure.
-
Use safe lifting practices to prevent both worker injuries and facility damage.
Having qualified personnel on the job ensures that each step of the move is carefully executed, protecting both workers and the facility.
5. Monitor and Control the Environment
A controlled environment minimizes unexpected risks during machinery moving. Keep these factors in mind:
-
Temperature and Humidity: In certain cases, extreme weather conditions or fluctuating temperatures can affect machinery or floor conditions. For example, wet floors may become slippery, increasing the risk of accidents.
-
Clear Work Zones: Keep the moving path clear of any tools, debris, or unnecessary items that could obstruct the move or cause accidents.
-
Safety Barriers: Establish work zone boundaries and use caution tape to keep non-essential personnel away from the moving area. This prevents accidental interference and protects both workers and machinery.
By controlling the environment and creating a safe zone, you protect both the moving process and your workers.
Best Practices for Minimizing Disruption
1. Schedule the Move During Off-Hours
Whenever possible, schedule the machinery move during off-peak hours or during scheduled downtime. This minimizes disruption to production processes and ensures workers aren’t exposed to unnecessary hazards during the move. Early planning and coordination help prevent any production delays.
2. Communicate with the Team
Effective communication is key to a smooth and efficient machinery move. Make sure everyone involved is aware of the moving plan, timelines, and any necessary precautions. Clear instructions and regular updates will help minimize confusion and ensure that no critical steps are overlooked.
3. Plan for Downtime Minimization
While some downtime is inevitable during machinery relocation, it can be minimized with careful coordination. Prepare backup plans to ensure that other parts of the operation continue without disruption. For instance, certain equipment might be relocated while other equipment remains functional to ensure continuous production.
4. Use Quality Moving Services
If the machinery move is large or particularly complex, it may be wise to consult with professional machinery movers. Companies like APS Industrial Services specialize in heavy machinery moving and have the expertise to execute moves without causing damage or disruption to your facility.
Trust APS Industrial Services for Your Machinery Move
At APS Industrial Services, we offer comprehensive machinery moving services designed to minimize facility damage and operational disruptions. Our team of highly trained rigging experts is equipped with state-of-the-art equipment to ensure your machinery move is safe, efficient, and seamless. From planning to execution, we ensure that your facility is fully protected throughout the process.
Contact us today for a consultation and learn how we can help with your next machinery move!
Newsletter
Don't miss a thing!
Sign up to receive daily news
Recent Posts
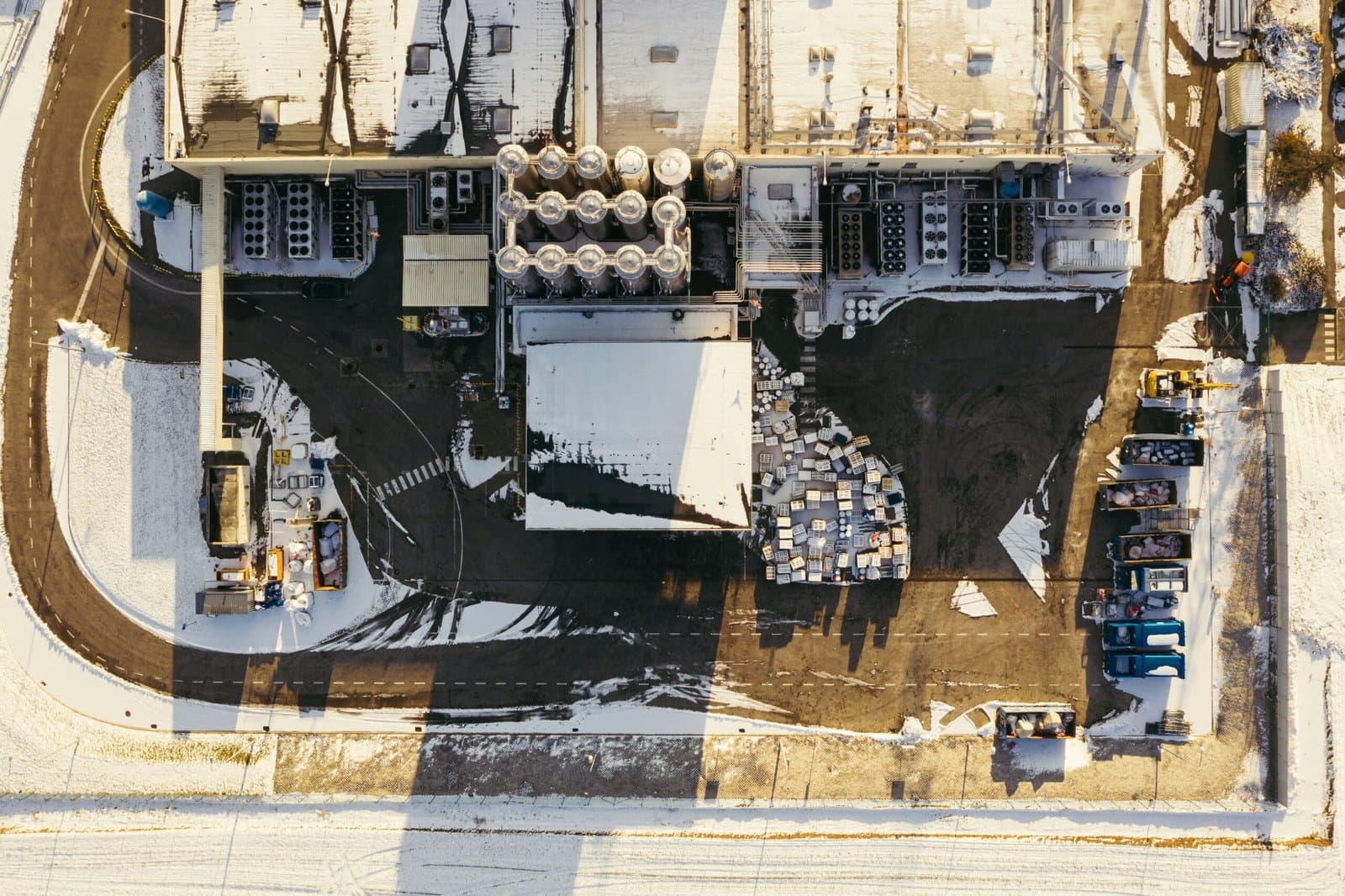
march 28, 2025
Industrial Facility Dismantling: Challenges & Solutions
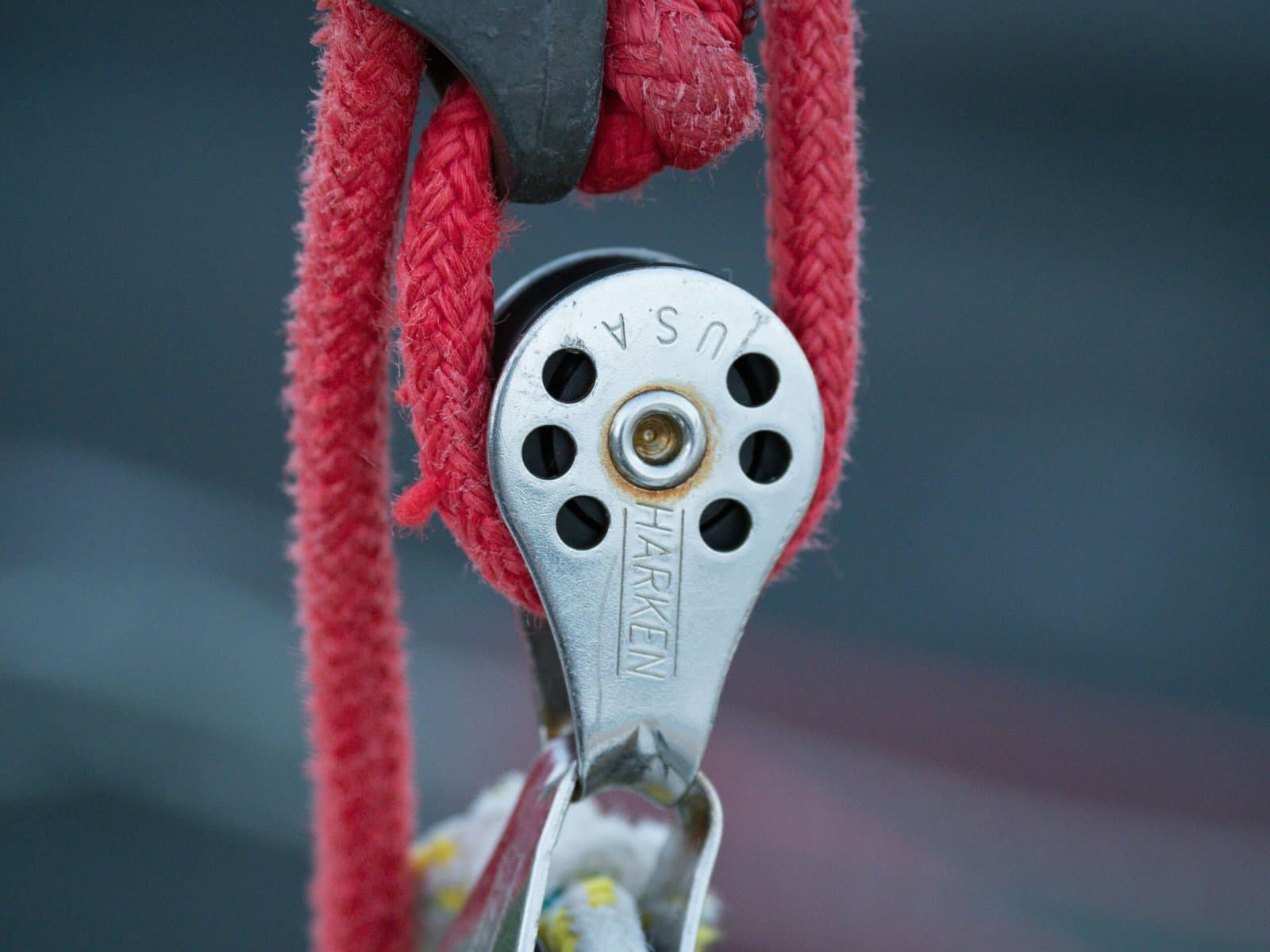
march 26, 2025
Machinery Moving: Proper Rigging for Safe Lifting & Transport
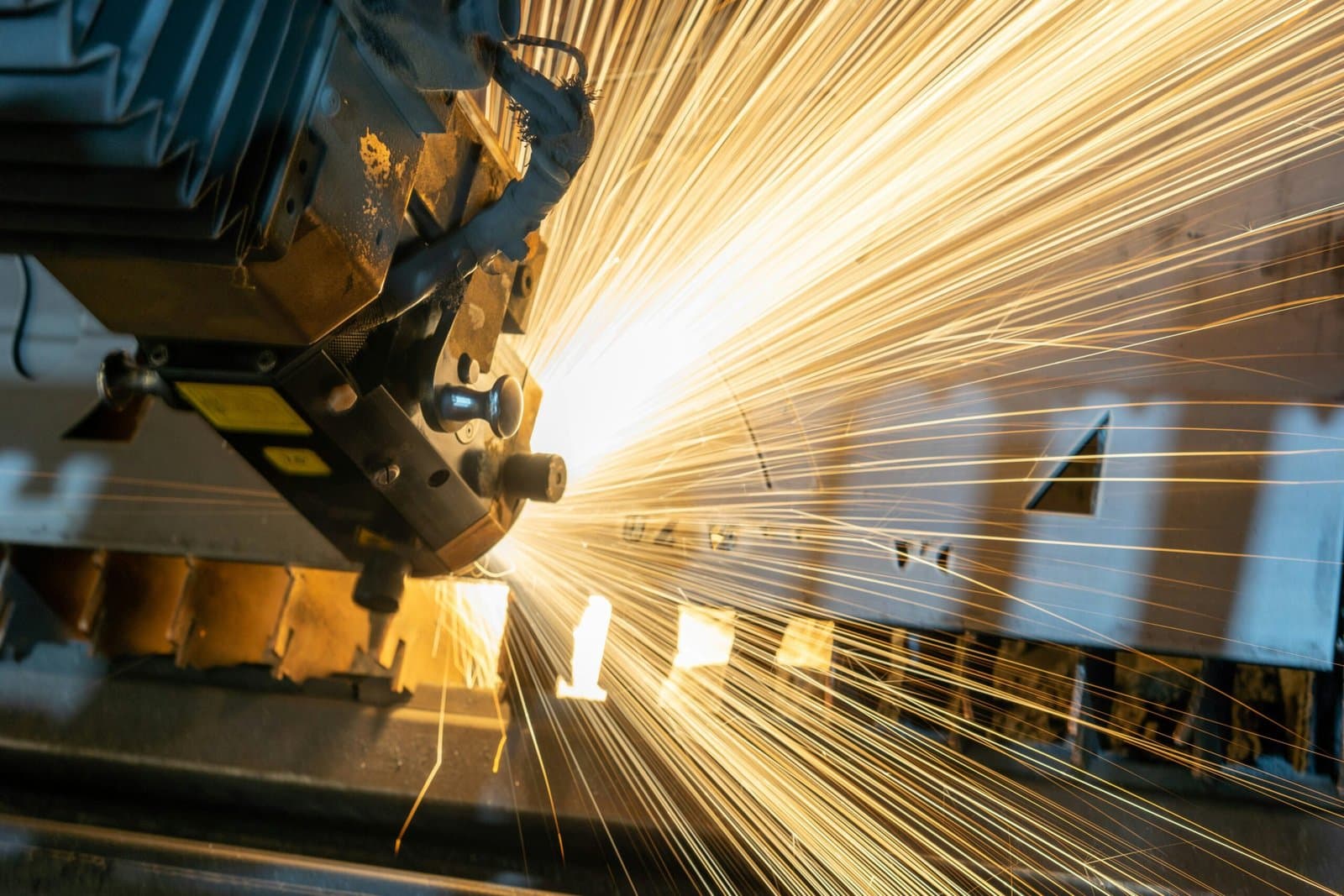
march 24, 2025
Manufacturing Rigging: Moving and Installing Heavy Machinery
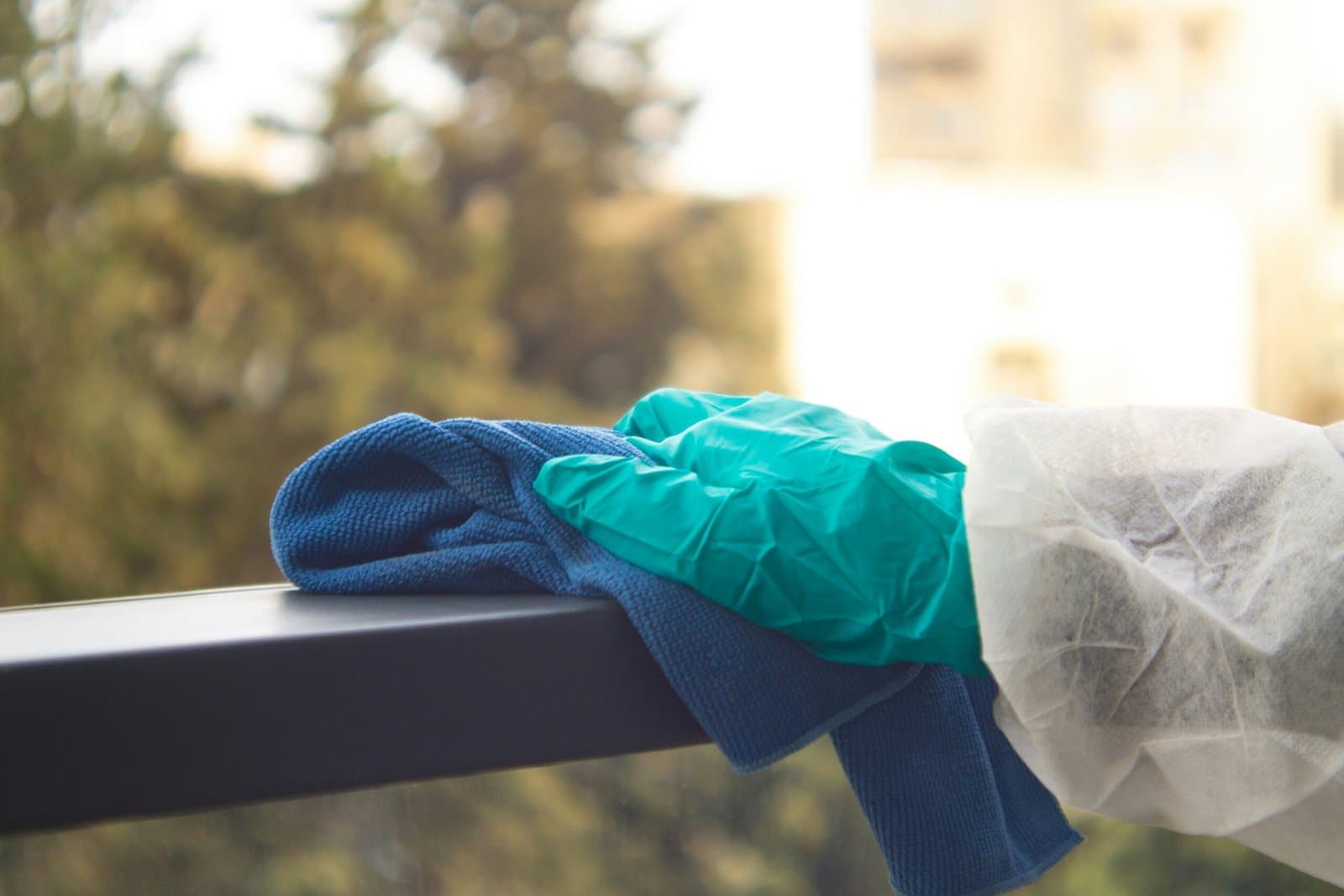
march 22, 2025
Commercial Office Cleaning: Enhancing Productivity & Employee Well-Being
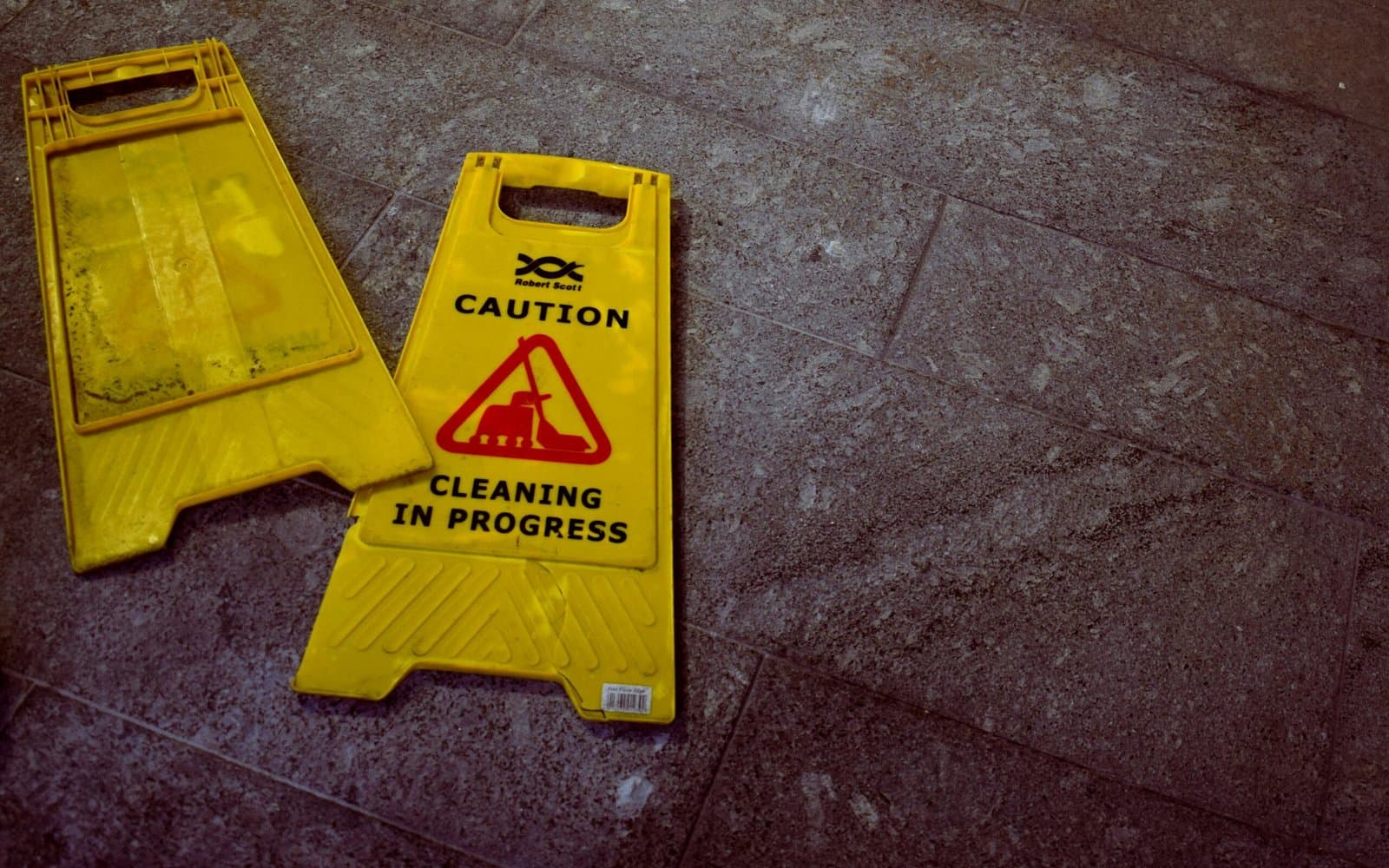
march 21, 2025