Industrial Stretch Wrappers – Tensile Strength, Pre-stretch, and More
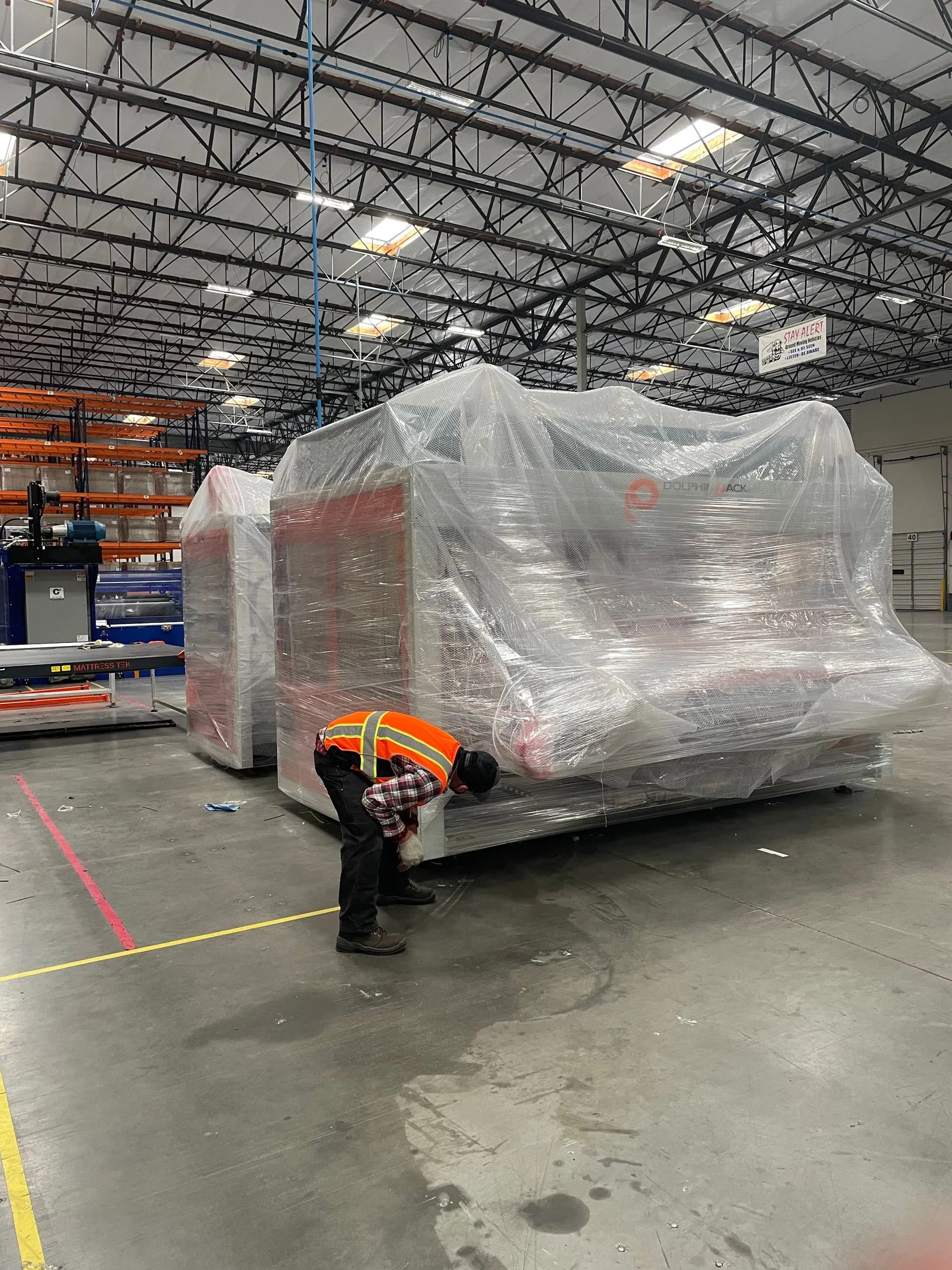
Industrial stretch wrapping plays a critical role in securing loads during transport and storage, reducing product damage and improving efficiency. For industry professionals, understanding the science behind these systems, especially concepts like tensile strength and pre-stretch, can help optimize load containment and reduce material costs. This blog explores the essential scientific principles behind industrial stretch wrappers, focusing on how tensile strength, pre-stretch, film gauge, and machine settings contribute to a well-balanced, cost-effective wrapping process.
The Role of Tensile Strength in Stretch Wrapping
Tensile strength refers to the maximum stress a material can withstand while being stretched before it breaks. For stretch film, tensile strength is vital because it ensures that the film can hold the load securely without tearing or breaking under strain. The key to a successful wrapping process lies in selecting the appropriate film with adequate tensile strength for the load being wrapped. Too low of a tensile strength could lead to film failure and load instability, while over-engineering with excessively high tensile strength can result in unnecessary costs.
For instance, films with lower tensile strength are suitable for lightweight packages, whereas high-tensile-strength films are essential for heavy, dense loads such as those encountered in industries like metal fabrication or construction.
Case Example: Metal Manufacturing
In a metal fabrication plant, dense loads require film with high tensile strength to prevent the film from breaking under stress. With the correct tensile strength, the company can secure heavy metal products on pallets without fear of the stretch film failing, ensuring safe transportation while minimizing damage.
Understanding Pre-stretch and Its Impact on Efficiency
Pre-stretch is another key factor in the stretch wrapping process. It refers to how much the stretch film is elongated before being applied to the load. Most stretch wrapping machines offer adjustable pre-stretch settings, which determine how far the film stretches before it wraps around the pallet. Pre-stretch plays a dual role in increasing the efficiency of the wrapping process and optimizing material usage.
For example, if a machine applies a 250% pre-stretch, the film will be elongated by 2.5 times its original length. This allows companies to use less film while maintaining effective load containment. However, setting the pre-stretch too high can lead to film tearing or inadequate containment force, while too low of a pre-stretch reduces cost efficiency.
Case Example: Food and Beverage Distribution
A beverage distributor optimized their pre-stretch settings on their automatic stretch wrapper to 250%. This adjustment led to a 35% reduction in film usage, which resulted in significant cost savings without compromising load stability during transit.
Film Gauge: Why Thickness Matters
The gauge or thickness of the stretch film determines how much force it can withstand and its overall durability. Film gauge selection is crucial, as thicker films (e.g., 80 gauge) offer more strength but are more expensive, while thinner films (e.g., 60 gauge) reduce costs but may compromise load security. A balance is needed based on the load’s weight, size, and fragility.
Machine stretch film is typically available in a range of gauges from 50 to 150+. The optimal film gauge depends on the industry, load type, and transport conditions. For example, a 70-gauge film may be ideal for lightweight consumer goods, while a 120-gauge film may be better for shipping heavy machinery.
Load Containment and Machine Settings
Correctly setting the machine’s tension, wrap force, and pre-stretch rate ensures the load is properly contained. Load containment is a measure of how securely the stretch film holds the load in place. When wrapping a pallet, the right machine settings prevent product shifting and toppling. If the tension is too high, the film may puncture or tear, leading to unstable loads. If too low, the load may shift during transit, causing damage to the goods.
For example, when wrapping irregular-shaped loads, machine settings need to be adjusted to ensure that all parts of the load receive adequate containment force without damaging the product.
Case Example: Pharmaceutical Industry
A pharmaceutical company dealing with sensitive medical supplies used stretch wrap machines with customizable tension settings. By reducing the wrap force, they ensured their delicate goods remained intact during transit, resulting in fewer damaged products and a higher level of customer satisfaction.
Conclusion: Optimizing Your Stretch Wrapping Process
Understanding the technical components of industrial stretch wrapping, from tensile strength to pre-stretch and film gauge, can significantly impact both load security and material efficiency. Professionals in industries like food and beverage, manufacturing, and pharmaceuticals can reduce costs and improve operational efficiency by selecting the right film and optimizing machine settings.
Looking to optimize your stretch wrapping process? Contact APS Industrial Services today for expert advice on selecting the right stretch film, machine settings, and more. Let us help you enhance efficiency and reduce costs across your operations.
Newsletter
Don't miss a thing!
Sign up to receive daily news
Recent Posts
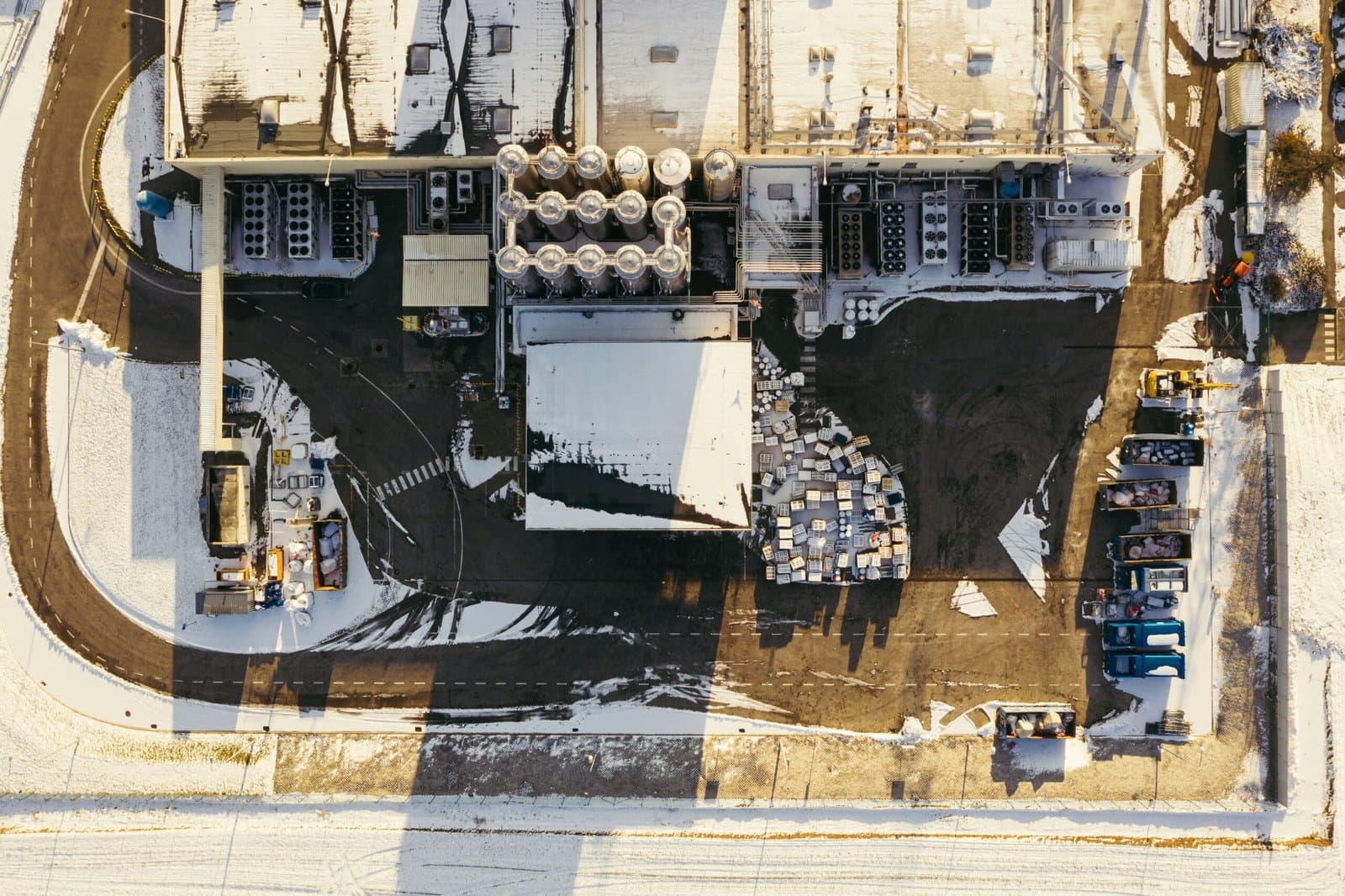
march 28, 2025
Industrial Facility Dismantling: Challenges & Solutions
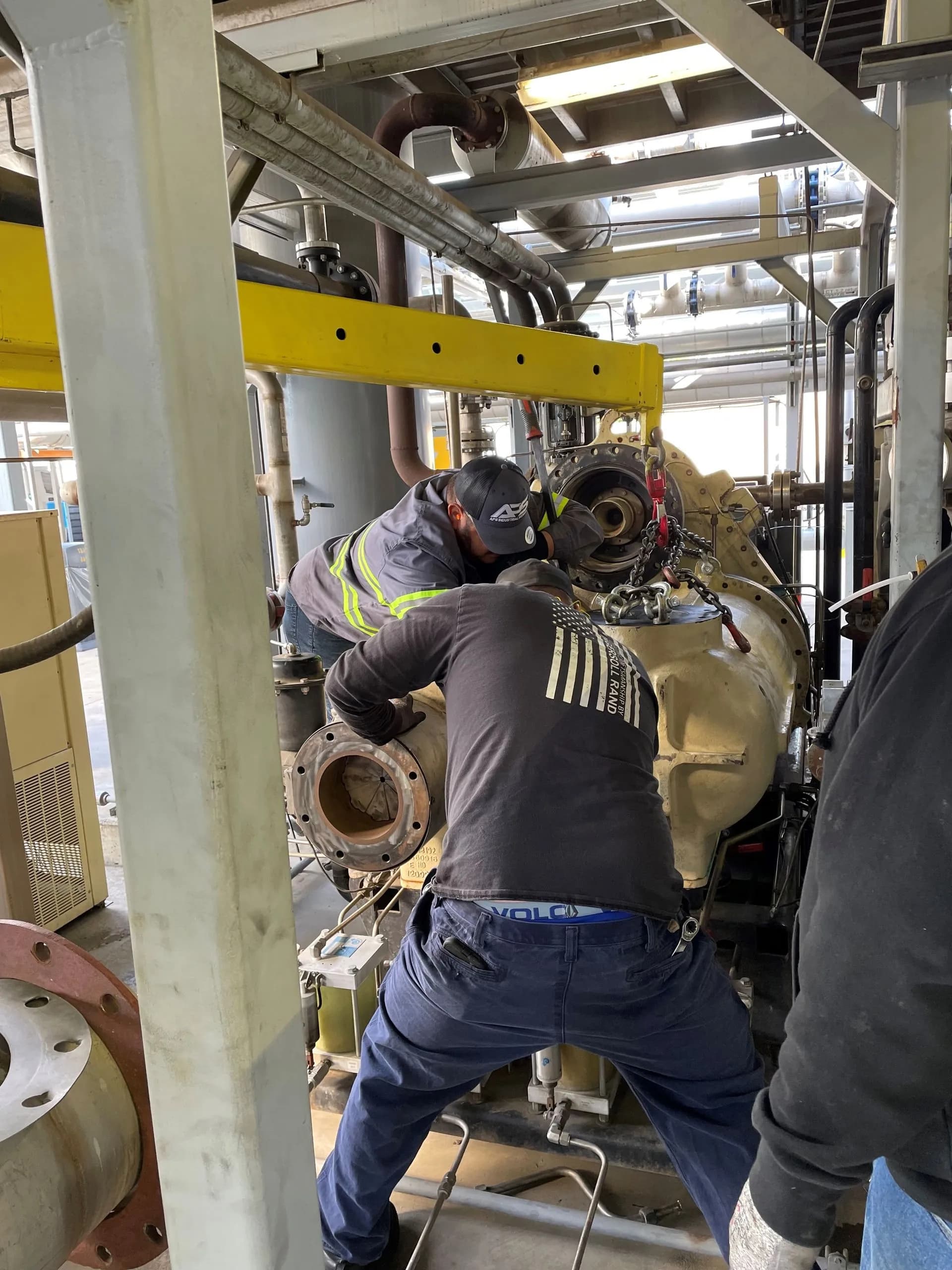
march 26, 2025
Machinery Moving: Protecting Your Facility
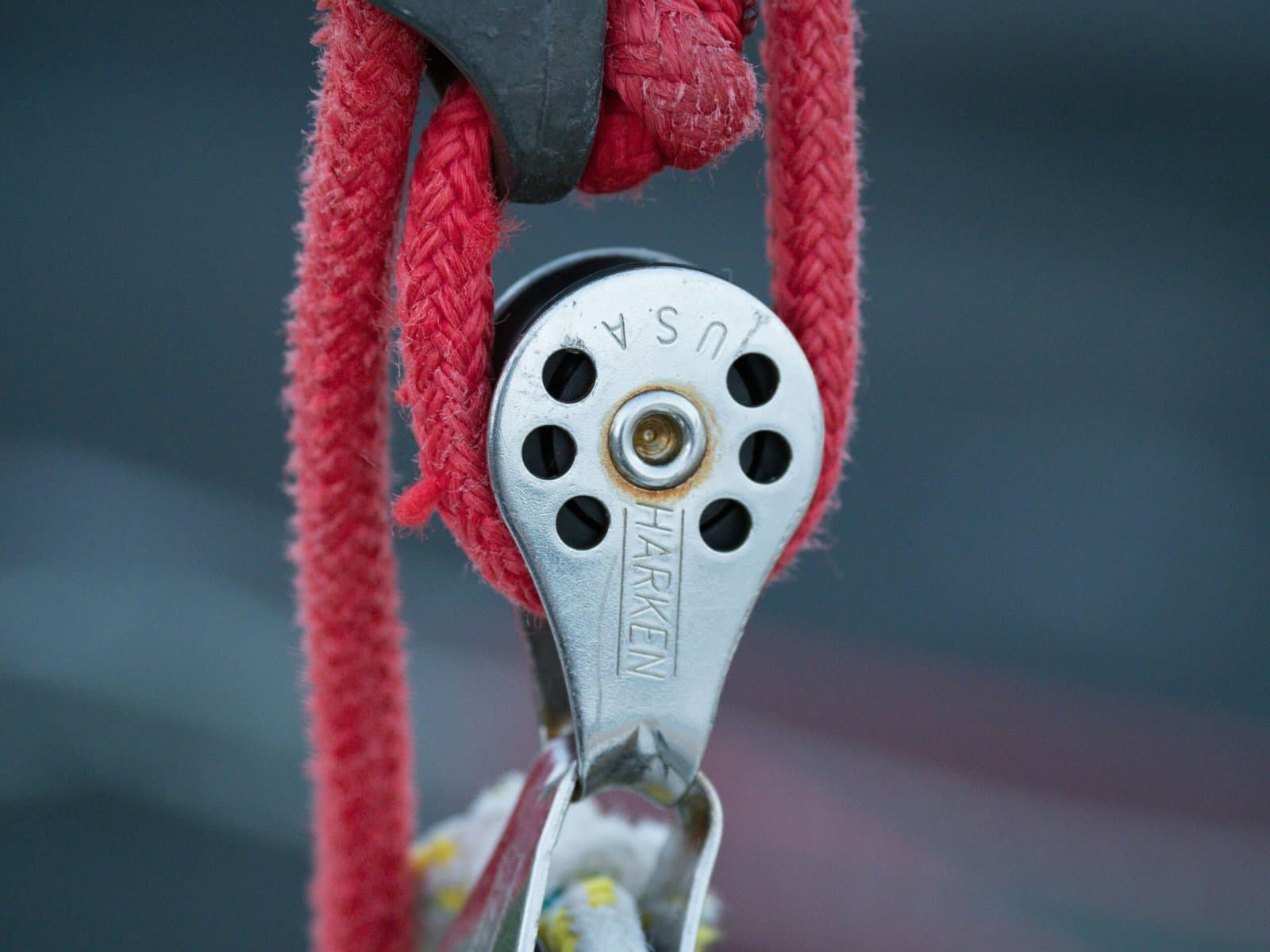
march 26, 2025
Machinery Moving: Proper Rigging for Safe Lifting & Transport
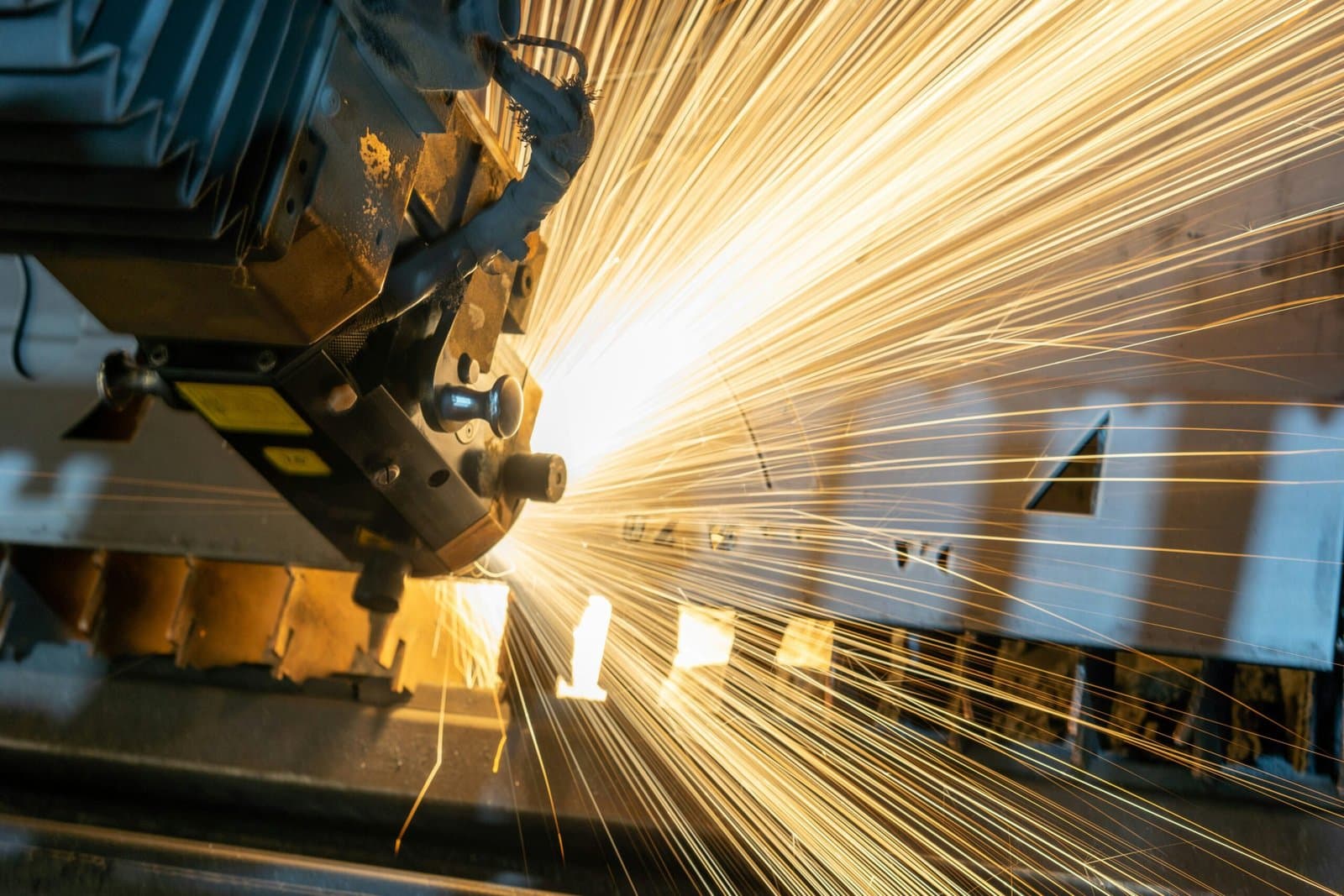
march 24, 2025
Manufacturing Rigging: Moving and Installing Heavy Machinery
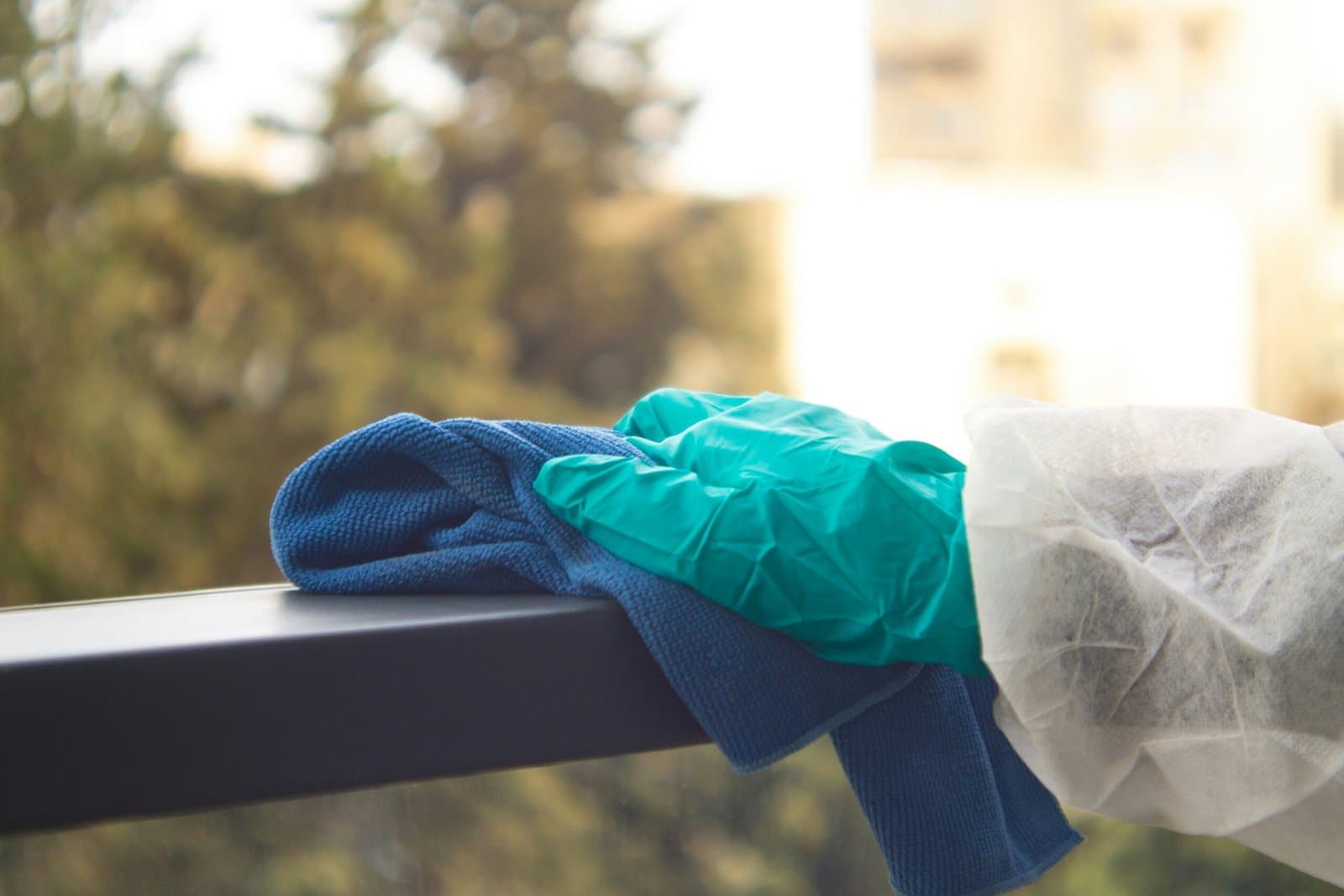
march 22, 2025
Commercial Office Cleaning: Enhancing Productivity & Employee Well-Being
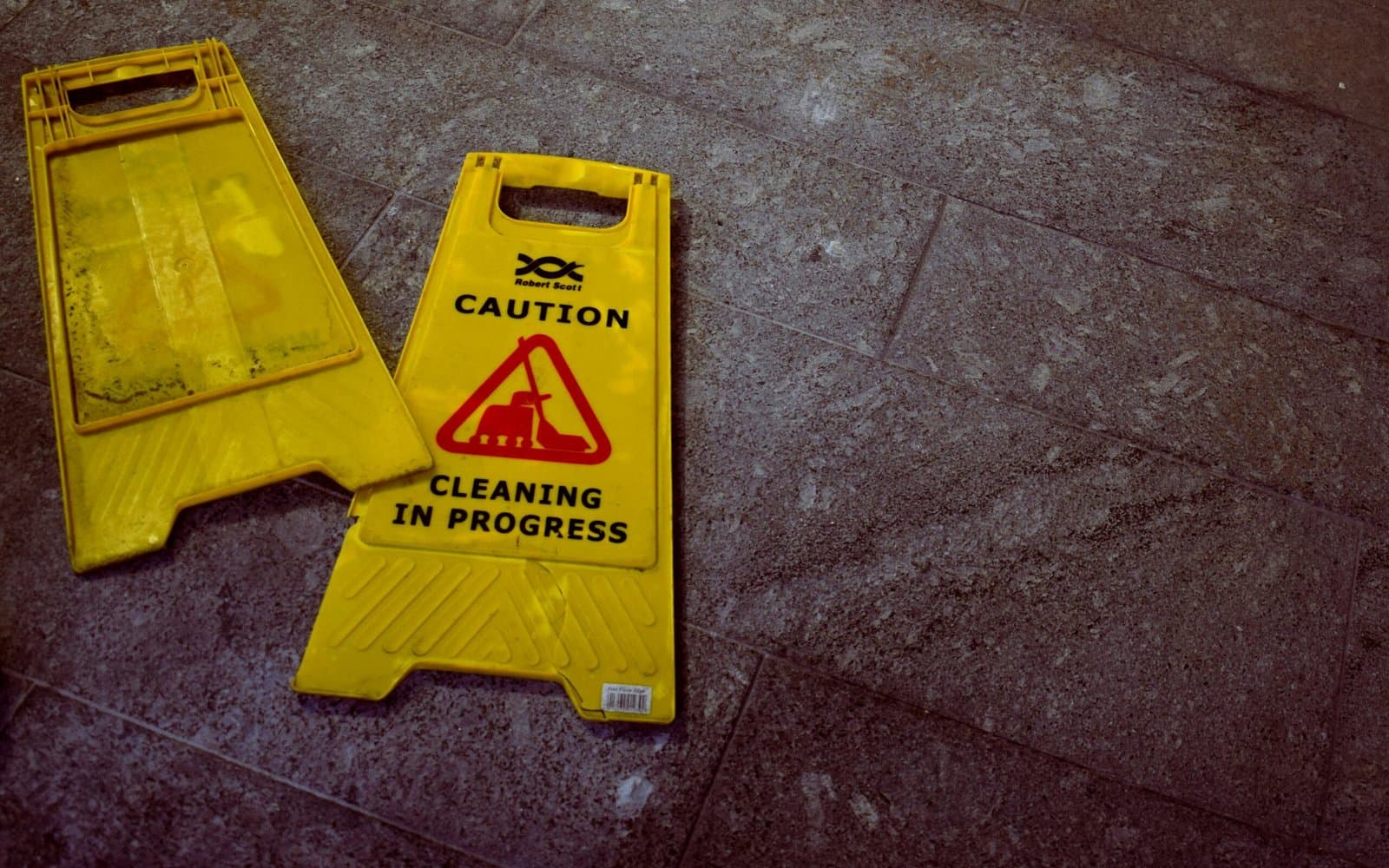
march 21, 2025